This document provides a comprehensive analysis of three primary aluminum product categories—Pure Aluminum, Wrought Aluminum Alloys, and Casting Aluminum Alloys—comparing their chemical compositions, physical properties, mechanical behaviors, advantages, applications, manufacturing processes, and cost-efficiency.
Aluminum is a lightweight, durable, and highly versatile metal that plays a crucial role in various industries due to its excellent properties, including corrosion resistance, high strength-to-weight ratio, and recyclability. Aluminum products are widely used in construction, transportation, packaging, electronics, and many other sectors.
Overview of Aluminum
Aluminum alloys are engineered materials combining aluminum (Al) with alloying elements to enhance mechanical, physical, and corrosion-resistant properties for specialized industrial applications. Below is a structured overview covering their composition, classification, properties, advantages, manufacturing, and key uses.
Pure Aluminum (99.0%–99.9999% Al)
Chemical Composition
- Primary Element: Aluminum (≥99.0%)
- Key Impurities:
- Fe + Si ≤ 1.0%
- Trace elements (Cu, Mn, Zn, etc.) ≤ 0.10% each
- Ultra-High Purity (UHP) Variants:
- 5N5 (99.9995% Al) – Used in semiconductor manufacturing.
6N (99.9999% Al) – Critical for nuclear and aerospace applications.
Mechanical Properties
- Tensile Strength: 10–15 MPa (soft annealed)
- Yield Strength: 5–10 MPa
- Elongation: 35–50%
- Hardness (Brinell): 15–20 HB
Physical Properties
Property | Value |
---|---|
Density | 2.70 g/cm³ |
Melting Point | 660.4°C |
Electrical Conductivity | 62% IACS (volume) |
Thermal Conductivity | 237 W/m·K |
Reflectivity (Visible Light) | >80% |
Corrosion Resistance | Excellent (passive oxide layer) |
Wrought Aluminum Alloys
- Processing Methods: Rolled, extruded, forged, or drawn.
- Alloy Series (Wrought):
Series Key Alloying Elements Example Alloys Typical Applications 1xxx Pure Al (≥99.0%) 1050, 1100 Chemical processing, foil, electrical conductors 2xxx Cu (2–6%) 2024, 2219 Aerospace structures, rocket casings, high-stress fittings 5xxx Mg (0.5–6.5%) 5052, 5083 Marine hulls, pressure vessels, automotive panels 6xxx Mg + Si (0.3–1.8%) 6061, 6063 Architectural extrusions, automotive frames, bicycle components 7xxx Zn (5–12%) + Mg + Cu 7075, 7475 Aircraft wings, high-performance bolts, military hardware
Key Alloy Series & Chemical Compositions
Alloy Series | Principal Alloying Elements | Example Alloys | Applications |
---|---|---|---|
1xxx | Pure Al (≥99.0%) | 1050, 1100 | Chemical equipment, foil |
2xxx | Cu (2–6%) | 2024, 2219 | Aircraft structures, rocket casings |
5xxx | Mg (0.5–6.5%) | 5052, 5083 | Marine structures, pressure vessels |
6xxx | Mg + Si (0.3–1.8%) | 6061, 6063 | Architectural extrusions, automotive frames |
7xxx | Zn (5–12%) + Mg + Cu | 7075, 7475 | Aerospace fittings, high-strength bolts |
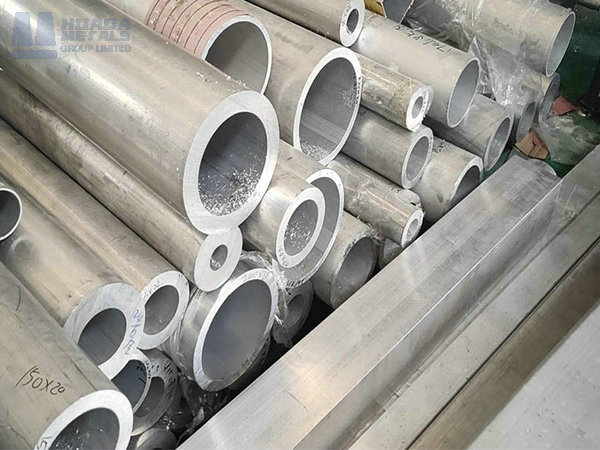
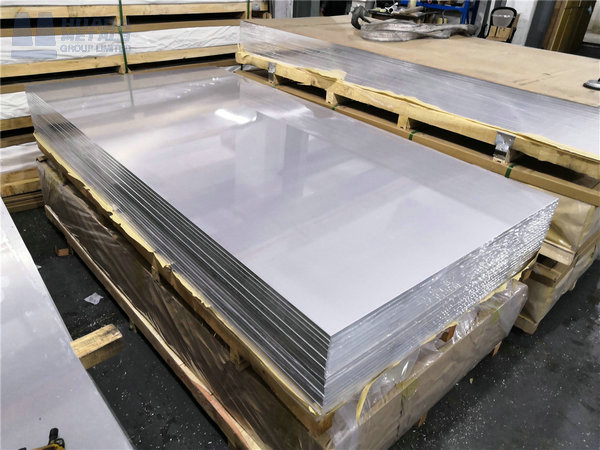
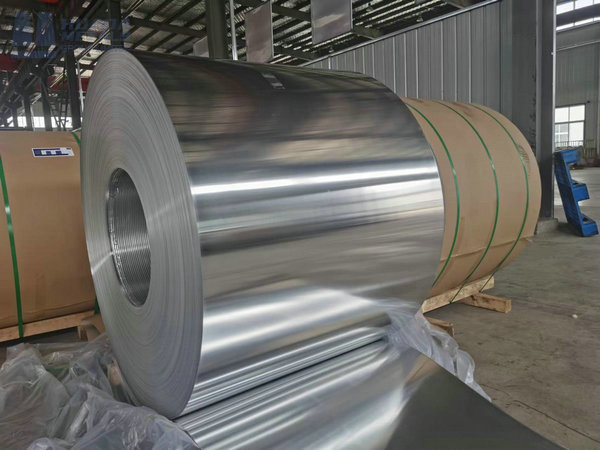
Mechanical Properties (T6 Temper)
Alloy Series | Tensile Strength (MPa) | Yield Strength (MPa) | Elongation (%) |
---|---|---|---|
1xxx | 110–140 | 45–70 | 20–30 |
2xxx | 470–520 | 390–450 | 10–15 |
5xxx | 220–270 | 170–220 | 15–20 |
6xxx | 290–320 | 240–270 | 12–18 |
7xxx | 570–620 | 500–550 | 8–12 |
Casting Aluminum Alloys
Key Alloy Families & Chemical Compositions
Alloy Family | Principal Alloying Elements | Example Alloys | Applications |
---|---|---|---|
Al-Si | Si (5–13%) | A356, 319 | Engine blocks, cylinder heads |
Al-Cu | Cu (3–11%) | 201.0, 224.0 | High-temp pistons, aircraft fittings |
Al-Mg | Mg (0.3–1.0%) | 520.0, 535.0 | Marine propellers, chemical tanks |
Al-Zn | Zn (4–12%) | ZA8, ZA12 | Die-cast gears, high-strength housings |
Mechanical Properties (As-Cast vs. T6 Temper)
Alloy Family | As-Cast UTS (MPa) | T6 UTS (MPa) | As-Cast Elongation (%) |
---|---|---|---|
Al-Si | 180–240 | 280–320 | 2–5 |
Al-Cu | 220–280 | 350–400 | 1–3 |
Al-Mg | 150–200 | 220–260 | 3–7 |
Al-Zn | 250–300 | 380–420 | 1–2 |
Advantages and Benifits of Aluminum
Common Aluminum Products
- Aluminum Sheets & Plates
Used in construction (roofing, cladding), automotive body panels, and aircraft structures.
Available in various alloys (e.g., 3003, 5052, 6061) for different strength requirements.
Aluminum Extrusions
Custom profiles for windows, doors, heat sinks, and structural frameworks.
Popular in architectural and industrial applications.
Aluminum Foil
Widely used in food packaging, insulation, and electronics.
Provides a moisture and oxygen barrier.
Aluminum Tubes & Pipes
Used in HVAC systems, hydraulic systems, and beverage cans.
Aluminum Castings
Die-cast parts for automotive engines, electronics housings, and machinery.
Aluminum Wire & Cables
Electrical transmission lines due to its conductivity and lightweight nature.
Aluminum Powder
Used in paints, pyrotechnics, and 3D printing.
- Design Flexibility: Complex geometries (e.g., engine blocks) with minimal machining.
- Cost-Effective: Near-net-shape production reduces material waste.
- High Fluidity: Al-Si alloys fill thin-walled molds effectively.
- Thermal Conductivity: Al-Si alloys excel in heat dissipation (e.g., automotive radiators).
- High Strength-to-Weight Ratio: Up to 3x stronger than pure Al.
- Workability: Excellent formability via rolling, extrusion, and forging.
- Corrosion Resistance: Enhanced by Mg (5xxx) or anodizing (6xxx).
- Heat Treatability: 2xxx, 6xxx, and 7xxx series strengthen via precipitation hardening.
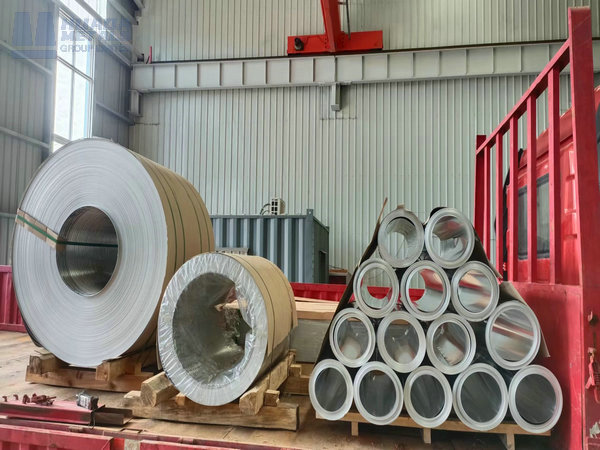
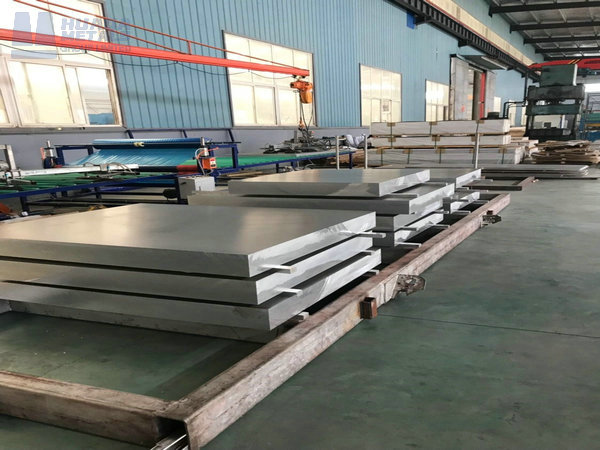
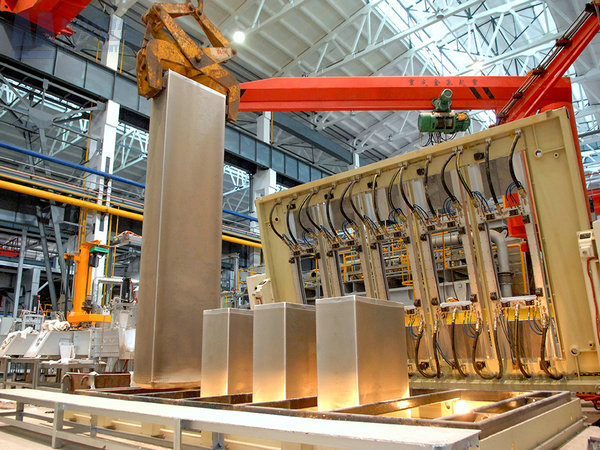
Industries of Application
- Aerospace: 7075-T6 for wing spars, 2024-T3 for fuselage skins.
- Automotive: 6061-T6 for chassis components, 5083-H116 for marine hulls.
- Construction: 6063-T5 for architectural extrusions.
- Automotive: A356-T6 for cylinder heads, ZA12 for transmission cases.
- Aerospace: Al-Cu alloys for turbine blades.
- Consumer Goods: Die-cast Al-Zn housings for electronics.
Comparision of Aluminum Types
Aluminum is one of the most sustainable metals, as recycling it saves ~95% of the energy required for primary production. The global aluminum industry continues to innovate in low-carbon production methods.
Metric | Pure Aluminum | Wrought Alloys | Casting Alloys |
---|---|---|---|
Strength | Low (10–15 MPa) | High (290–620 MPa) | Moderate (150–420 MPa) |
Formability | Excellent (foil, sheet) | Excellent (extrusions) | Limited (near-net-shape) |
Corrosion Resistance | Excellent | Good (with anodizing) | Moderate (requires coatings) |
Cost/kg | $2.0–2.5 | $2.5–3.5 | $2.0–3.0 (tooling cost) |
Lead Time | Short (foil) | Moderate (extrusions) | Long (die casting setup) |
Manufacturing Process & Cost of Aluminum
- Process:
- DC Casting → Homogenization → Hot Rolling → Cold Working → Solution Heat Treatment (Quenching) → Aging.
- Cost: Moderate (higher than pure Al but lower than cast alloys for complex shapes).
- Process: Direct chill casting (DC), followed by rolling/extrusion for thin foils.
- Cost: Lowest among aluminum variants due to minimal alloying.
In Conclusion
Aluminum products are essential in modern life, offering a perfect balance of strength, lightness, and sustainability. With ongoing advancements in alloy technology and green manufacturing, aluminum remains a cornerstone material for future innovations.
- Pure Aluminum dominates in electrical, optical, and decorative applications where conductivity and corrosion resistance are paramount.
- Wrought Alloys excel in high-strength, load-bearing structures (aerospace, automotive) due to their workability and heat treatability.
- Casting Alloys offer cost-effective, complex geometries for automotive, industrial, and consumer goods, balancing strength and manufacturability.
By selecting the appropriate aluminum variant based on performance requirements, cost constraints, and manufacturing feasibility, engineers can optimize designs across industries.