Carbon steel is a fundamental iron-carbon alloy containing up to 2.1% carbon by weight, with small amounts of manganese, silicon, and other trace elements. It is one of the most widely used materials in construction, manufacturing, and engineering due to its high strength, durability, and cost-effectiveness.
Carbon steel, a fundamental alloy in engineering and manufacturing, is composed primarily of iron (Fe) and carbon (C), with trace elements like silicon (Si), manganese (Mn), sulfur (S), and phosphorus (P). Its properties vary significantly with carbon content, leading to classifications into low-carbon (≤0.30% C), medium-carbon (0.30–0.60% C), and high-carbon (≥0.60% C) steels. This analysis explores its chemical composition, physical/mechanical properties, advantages, applications, manufacturing processes, and cost-effectiveness, supported by comparative tables and case studies.
Classification of Carbon Steel
Carbon steel is categorized based on its carbon content, which determines its mechanical properties and applications.
Type | Carbon Content (%) | Characteristics | Common Applications |
---|---|---|---|
Low Carbon Steel (Mild Steel) | 0.05% – 0.25% | Soft, ductile, easy to weld & form | Automotive panels, wires, pipes, structural beams |
Medium Carbon Steel | 0.25% – 0.60% | Balanced strength & ductility, heat-treatable | Gears, axles, machinery parts, railway tracks |
High Carbon Steel | 0.60% – 1.00% | Very hard & strong, but brittle | Knives, cutting tools, springs, high-strength wires |
Ultra-High Carbon Steel | 1.00% – 2.10% | Extremely hard, poor ductility | Specialty tools, blades, industrial wear parts |
Chemical Composition of Carbon Steel
Classification | Carbon Content (%) | Key Alloying Elements | Typical Applications |
---|---|---|---|
Low-Carbon (Mild) Steel | ≤0.30 | Mn (0.3–1.2%), Si (≤0.4%) | Automotive body panels, structural beams, pipes |
Medium-Carbon Steel | 0.30–0.60 | Mn (0.6–1.6%), Cr (≤0.5%) | Gear components, crankshafts, railway tracks |
High-Carbon Steel | ≥0.60 | Mn (0.6–1.0%), W (≤0.5%) | Cutting tools, springs, high-strength wires |
- Trace Elements:
- Sulfur (S): Enhances machinability but reduces ductility (typically ≤0.05%).
- Phosphorus (P): Increases strength but worsens toughness (typically ≤0.04%).
- Chromium (Cr) & Nickel (Ni): Added in trace amounts (≤0.3%) to improve corrosion resistance in wet steam environments.
Physical Properties of Carbon Steel
- Density: ~7.85 g/cm³ (consistent across carbon ranges).
- Thermal Conductivity: ~45 W/(m·K) (lower than aluminum/copper but adequate for structural applications).
- Melting Point: 1,370–1,530°C (varies with carbon content).
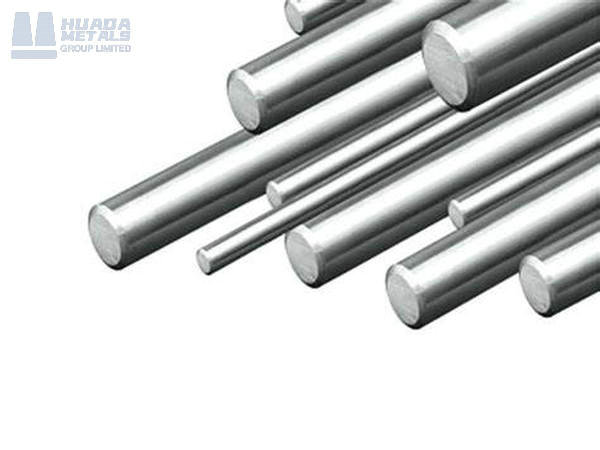
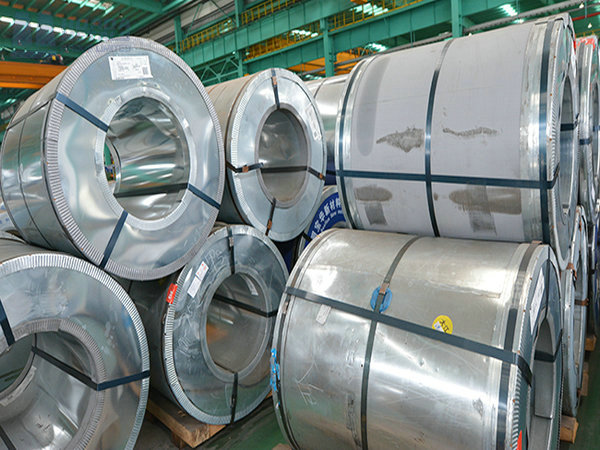
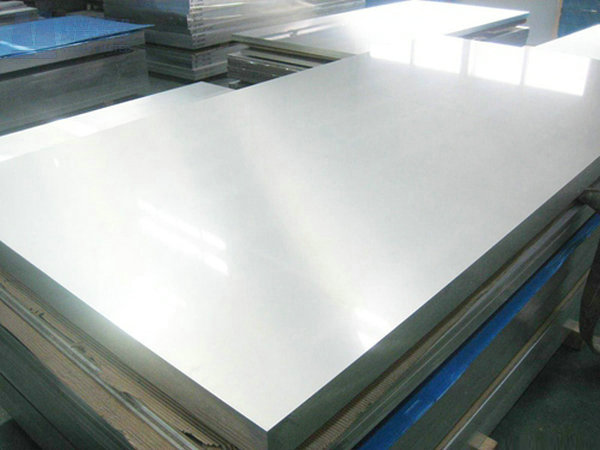
Mechanical Properties
Property | Low-Carbon Steel | Medium-Carbon Steel | High-Carbon Steel |
---|---|---|---|
Tensile Strength | 370–550 MPa | 550–850 MPa | 850–1,200 MPa |
Yield Strength | 200–350 MPa | 350–550 MPa | 550–900 MPa |
Elongation (%) | 25–35 | 15–25 | 5–15 |
Hardness (Brinell) | 100–150 HB | 150–220 HB | 220–300 HB |
Advantages & Key Characteristics of Carbon Steel
- Cost-Effectiveness:
- Raw materials (iron ore, coal) are abundant, reducing production costs by 30–50% compared to stainless steel.
- Example: A medium-carbon steel gear costs 2–5/kg∗∗vs.∗∗15–30/kg for alloy steel.
- High Strength-to-Weight Ratio:
- Medium-carbon steel (0.45% C) achieves 700 MPa UTS at 7.85 g/cm³ density, outperforming aluminum alloys (e.g., 6061-T6: 310 MPa UTS at 2.7 g/cm³).
- Weldability & Machinability:
- Low-carbon steel (e.g., AISI 1018) is easily welded and machined, making it ideal for automotive frames.
- Recyclability:
- Over 90% of carbon steel is recyclable, minimizing environmental impact.
Applications & Case Studies of Carbon Steel
Industry | Application Example | Material Grade | Key Requirements Met |
---|---|---|---|
Automotive | Engine crankshaft | AISI 1045 (0.45% C) | High fatigue strength, machinability |
Construction | Skyscraper structural beams | ASTM A36 (0.26% C) | Ductility, weldability, cost efficiency |
Tooling | Drill bits | AISI W1 (0.7–1.0% C) | Hardness (60–65 HRC), wear resistance |
Energy | Pressure vessel (nuclear) | SA-516 Gr. 70 (0.28% C, 0.035% S) | Stress corrosion resistance, high toughness |
- Case Study: AISI 1045 Crankshaft
- Process: Forging + quenching + tempering.
- Performance: Achieves 700 MPa UTS and 15% elongation, balancing strength and ductility.
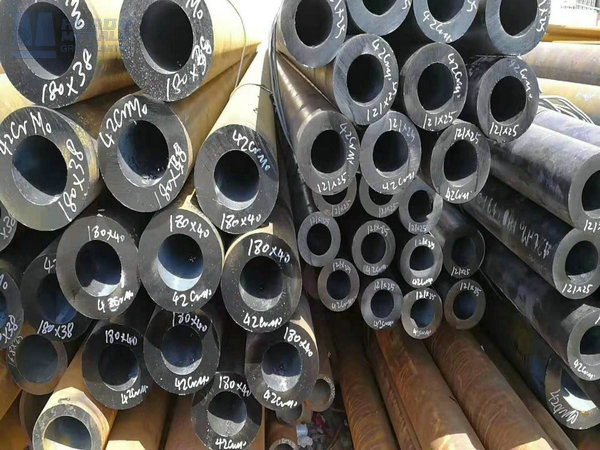
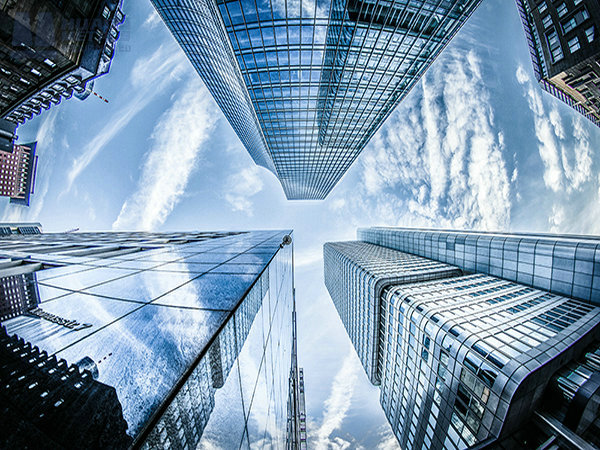
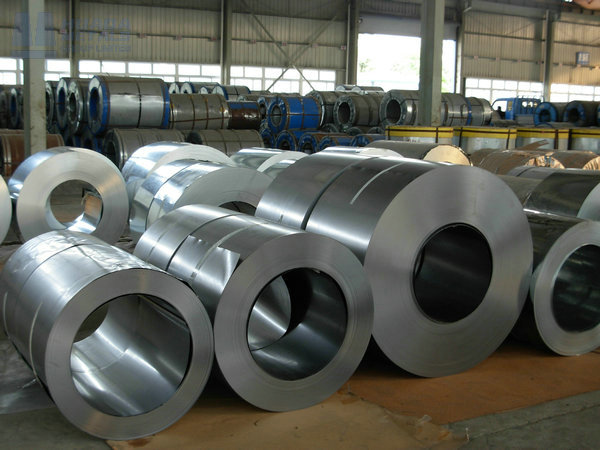
Manufacturing Processes & Costs of Carbon Steel
A. Primary Production Routes
- Blast Furnace (BF) + Basic Oxygen Furnace (BOF):
- Cost: $400–600/ton (long process, high-volume).
- Emissions: 1.8–2.2 tons CO₂/ton steel.
- Electric Arc Furnace (EAF):
- Cost: $500–700/ton (short process, 90% scrap-based).
- Emissions: 0.5–1.0 tons CO₂/ton steel.
B. Secondary Processing
- Hot Rolling: Reduces billet thickness (e.g., 250 mm → 3 mm sheet).
- Cold Drawing: Improves surface finish (e.g., wire production).
C. Total Cost Breakdown
Component | Cost Contribution (%) |
---|---|
Raw Materials | 45 |
Energy | 25 |
Labor | 15 |
Overheads | 15 |
Comparative Analysis: Carbon Steel vs. Alternative Materials
Metric | Carbon Steel (AISI 1045) | Stainless Steel (304) | Aluminum Alloy (6061-T6) |
---|---|---|---|
Cost ($/kg) | $0.8–1.2 | $2.5–4.0 | $2.0–3.5 |
Tensile Strength (MPa) | 700 | 520 | 310 |
Density (g/cm³) | 7.85 | 8.0 | 2.7 |
Corrosion Resistance | Poor (requires coating) | Excellent | Moderate (anodizing needed) |
- Best Use Cases:
- Carbon Steel: High-load, non-corrosive environments (e.g., construction, automotive).
- Stainless Steel: Corrosive environments (e.g., marine, food processing).
- Aluminum Alloy: Lightweight, non-structural applications (e.g., aerospace, electronics).
In Conclusion
Carbon steel remains indispensable due to its cost-effectiveness, mechanical versatility, and recyclability. While its susceptibility to corrosion limits use in harsh environments, advancements in coating technologies (e.g., Ni-W electroplating) and alloying (e.g., Cr/Ni trace additions) expand its applicability. Manufacturers must weigh performance requirements, budget constraints, and sustainability goals when selecting materials.
For cost-sensitive, high-strength applications, carbon steel is unmatched. For corrosion-resistant or lightweight needs, alternatives like stainless steel or aluminum may be preferable.