Stainless steel is a corrosion-resistant alloy of iron (Fe), chromium (Cr), and other elements, distinguished by its ability to form a passive oxide layer (Cr₂O₃) that prevents rusting. Classified into austenitic, ferritic, martensitic, duplex, and precipitation-hardened (PH) grades, it serves industries ranging from construction to aerospace. This analysis explores its chemical composition, physical/mechanical properties, advantages, applications, manufacturing processes, and cost-benefit trade-offs, supported by comparative tables and case studies.
Stainless steel is a corrosion-resistant iron alloy containing a minimum of 10.5% chromium, along with nickel, molybdenum, and other elements. It is widely used in industries requiring hygiene, durability, and aesthetic appeal, such as food processing, medical, construction, and automotive.
Overview of Stainless Steel
Stainless steel’s performance hinges on its chromium content (≥10.5%) and alloy modifications:Trace Elements:
- Nickel (Ni): Stabilizes austenite (e.g., 304: 8–10.5% Ni).
- Molybdenum (Mo): Enhances pitting resistance (e.g., 316: 2–3% Mo).
- Nitrogen (N): Increases strength (e.g., 316LN: 0.1–0.22% N).
Chemical Composition & Classification
Stainless Steel Family | Key Alloying Elements | Microstructure | Typical Applications |
---|---|---|---|
Austenitic (300 Series) | Cr (16–26%), Ni (6–22%), N (≤0.25%) | FCC (γ-phase) | Food processing, architecture, medical devices |
Ferritic (400 Series) | Cr (10.5–30%), C (≤0.03%) | BCC (α-phase) | Automotive exhausts, home appliances, indoor architecture |
Martensitic (400 Series) | Cr (11.5–18%), C (0.1–1.2%) | Body-centered tetragonal (BCT) | Cutting tools, surgical instruments, turbine blades |
Duplex (2205, 2507) | Cr (21–25%), Ni (4.5–7%), Mo (2.5–3.5%) | 50:50 α/γ-phase | Oil & gas pipelines, chemical plants, marine structures |
Precipitation-Hardened (17-4 PH) | Cr (15–17.5%), Ni (3–5%), Cu (3–5%) | Martensitic/austenitic (heat-treated) | Aerospace components, nuclear parts, high-wear tools |
Physical Properties of Stainless Steel
Type | Key Composition | Characteristics | Common Applications |
---|---|---|---|
Austenitic (300 Series) | Fe + Cr (16-26%) + Ni (6-22%) | Non-magnetic, excellent corrosion resistance, formable & weldable | Kitchenware, chemical tanks, medical implants |
Ferritic (400 Series) | Fe + Cr (10.5-30%) + little/no Ni | Magnetic, moderate corrosion resistance, lower cost | Automotive exhausts, industrial equipment |
Martensitic (400 Series) | Fe + Cr (12-18%) + C (0.1-1.2%) | Hard & strong, heat-treatable, magnetic | Knives, turbine blades, surgical tools |
Duplex (Mixed Austenitic-Ferritic) | Fe + Cr (18-28%) + Ni (4.5-8%) + Mo (2.5-4%) | High strength, excellent corrosion resistance | Oil & gas pipelines, desalination plants |
Precipitation-Hardening (PH Grades) | Fe + Cr + Ni + Cu/Al/Ti | Ultra-high strength, heat-treatable | Aerospace components, nuclear reactors |
- Density: 7.7–8.0 g/cm³ (similar to carbon steel but higher than aluminum).
- Thermal Conductivity: 15–25 W/(m·K) (lower than carbon steel, requiring thermal design adjustments).
- Melting Point: 1,375–1,530°C (varies with alloy composition).
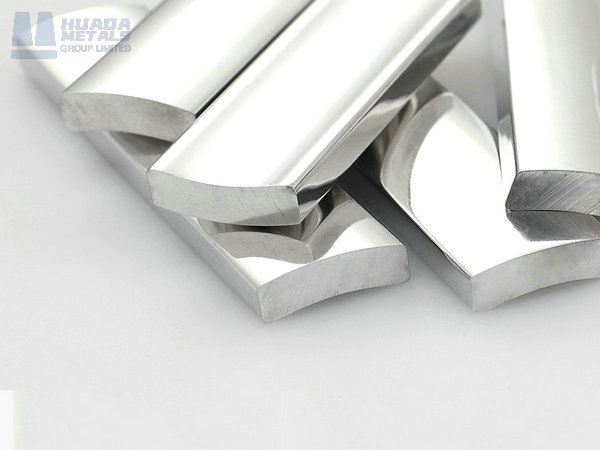
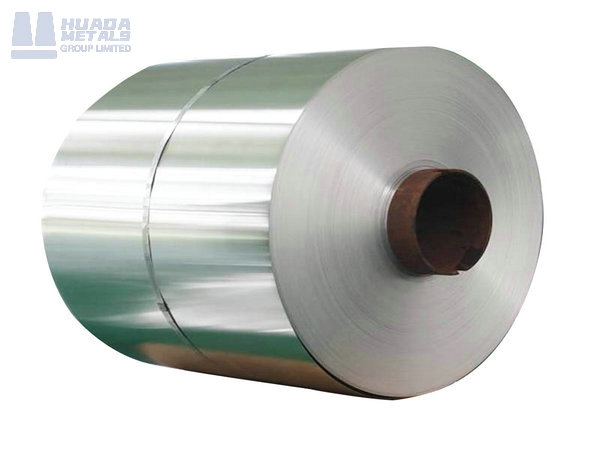
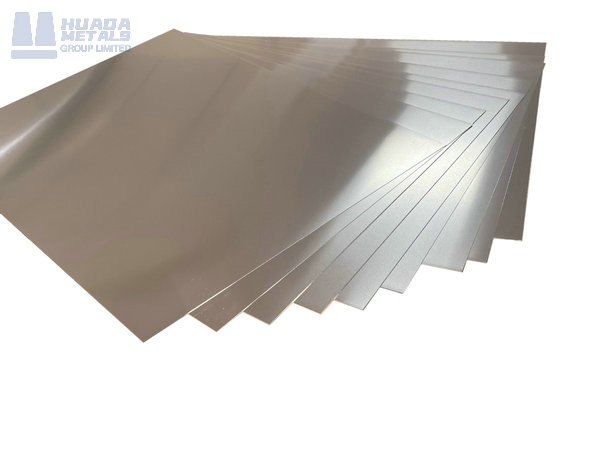
Mechanical Properties of Stainless Steel
Property | Austenitic (304) | Ferritic (430) | Martensitic (440C) | Duplex (2205) |
---|---|---|---|---|
Tensile Strength | 515–720 MPa | 450–600 MPa | 760–860 MPa | 620–880 MPa |
Yield Strength | 205–310 MPa | 205–310 MPa | 520–760 MPa | 450–655 MPa |
Elongation (%) | 40–60 | 22–25 | 8–12 | 25–35 |
Hardness (Rockwell) | B80–B95 | C30–C45 | C56–C60 | C32–C38 |
Corrosion Resistance | Excellent (Pitting Resistance Equivalent Number, PREN ≥ 19) | Moderate (PREN 16–18) | Good (PREN ≥ 20, with Mo) | Exceptional (PREN ≥ 34) |
- Heat Treatment Effects:
- Solution Annealing (Austenitic): Heated to 1,040–1,150°C to dissolve carbides (e.g., 304).
- Martensitic Hardening: Austenitized (1,000–1,050°C) + oil/air quenching + tempering (e.g., 440C: 150–300°C for HRC 58–60).
- PH Steel Aging: Solution-treated + aged (480–620°C) for precipitation strengthening (e.g., 17-4 PH: H900 condition, 1,310 MPa UTS).
Advantages & Key Characteristics of Stainless Steel
- Superior Corrosion Resistance:
- Austenitic (316L): Withstands chlorides (e.g., seawater, medical implants) due to Mo addition (PREN ≥ 24).
- Duplex (2205): Combines ferritic pitting resistance and austenitic toughness for marine use.
- High-Temperature Strength:
- Ferritic (446): Maintains strength up to 1,100°C (used in furnace components).
- Aesthetic & Hygienic Properties:
- Austenitic (304/316): Non-porous, easy-to-clean surfaces for food/pharmaceutical industries.
- Recyclability:
- Over 92% of stainless steel is recyclable, with scrap retaining 100% of its mechanical properties.
Applications & Case Studies of Stainless Steel
A. Austenitic (304, 316)
Food Industry – Kitchen sinks, cutlery, processing equipment.
Medical – Surgical instruments, implants.
Architecture – Elevators, facades, handrails.
B. Ferritic (430, 409)
Automotive – Exhaust systems, trim parts.
Industrial – Heat exchangers, washing machine drums.
C. Martensitic (410, 420)
Cutlery – Chef knives, scissors.
Industrial Tools – Bearings, valves.
D. Duplex (2205, 2507)
Chemical & Oil Industry – Pipes, pressure vessels.
Marine – Shipbuilding, desalination plants.
Industry | Application Example | Material Grade | Key Requirements Met |
---|---|---|---|
Architecture | Burj Khalifa cladding | 316L (austenitic) | Corrosion resistance, aesthetics |
Oil & Gas | Subsea pipelines | 2205 (duplex) | High strength, chloride pitting resistance |
Medical | Surgical scalpels | 440C (martensitic) | Hardness (HRC 58–60), edge retention |
Aerospace | Landing gear bearings | 17-4 PH (PH) | High strength (1,240 MPa UTS), fatigue resistance |
Automotive | Exhaust manifolds | 409 (ferritic) | Oxidation resistance, cost-efficiency |
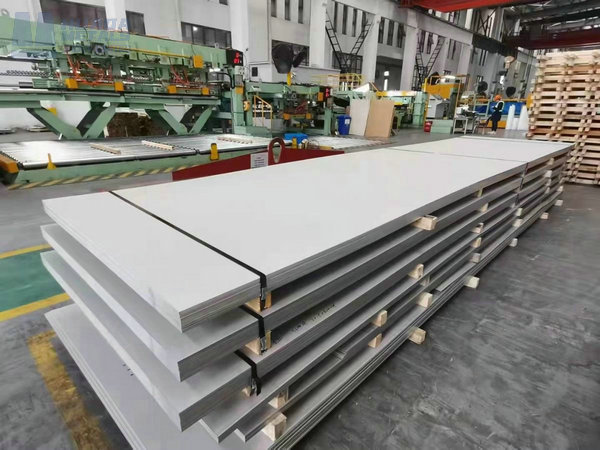
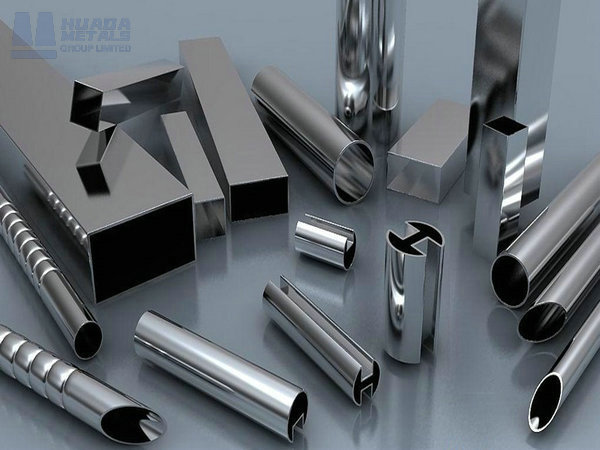
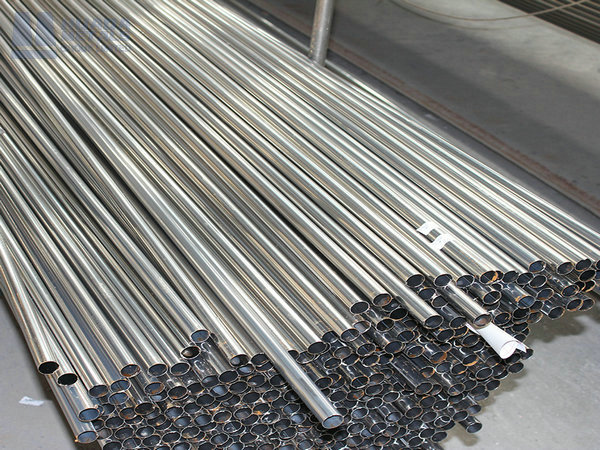
Manufacturing Processes & Costs of Stainless Steel
A. Primary Production Routes
- Electric Arc Furnace (EAF) + Argon Oxygen Decarburization (AOD):
- Cost: $2,500–4,000/ton (short process, 90% scrap-based).
- Emissions: 0.8–1.5 tons CO₂/ton steel (lower than carbon steel’s 1.8–2.2 tons).
- Electroslag Remelting (ESR):
- Cost: $6,000–10,000/ton (for PH/martensitic grades requiring ultra-low impurities).
B. Secondary Processing
- Cold Rolling: Improves surface finish (e.g., 2B finish for 304).
- Electropolishing: Reduces surface roughness (Ra < 0.1 μm) for medical devices.
C. Total Cost Breakdown
Component | Cost Contribution (%) |
---|---|
Raw Materials | 55 |
Energy | 20 |
Alloying Additives | 15 |
Labor & Overheads | 10 |
Stainless Steel vs. Carbon Steel vs. Alloy Steel
Property | Stainless Steel | Carbon Steel | Alloy Steel |
---|---|---|---|
Corrosion Resistance | Excellent (due to Cr) | Poor (rusts easily) | Moderate (depends on alloy) |
Strength | Moderate to High | High (heat-treated) | Very High (customizable) |
Cost | High | Low | Medium to High |
Machinability | Difficult (work-hardens) | Excellent (low carbon) | Moderate |
Magnetic? | Mostly non-magnetic (except ferritic/martensitic) | Yes | Depends on alloy |
Common Uses | Medical, food processing, architecture | Construction, machinery, tools | Aerospace, automotive, high-stress parts |
In Conclusion
Stainless steel is a versatile, corrosion-resistant, and durable material essential in modern industry. Its different grades allow for specialized uses, from surgical scalpels to skyscraper cladding. While costlier than carbon steel, its longevity and low maintenance justify the investment.
Stainless steel’s corrosion resistance, hygienic properties, and recyclability make it indispensable for critical industries. While its higher cost (2.5–4.0/kg vs. carbon steel’s 0.8–1.2/kg) restricts use to specialized applications, advancements in nitrogen-alloying (e.g., 316LN) and duplex steel development enhance cost-performance trade-offs.
For corrosive, high-purity, or aesthetic applications, stainless steel is unparalleled. For cost-sensitive, non-corrosive needs, carbon steel or aluminum may be preferable.