Incoloy alloys, a registered trademark of Special Metals Corporation, represent a family of nickel-iron-chromium-based superalloys engineered for exceptional corrosion resistance, high-temperature strength, and mechanical durability. These alloys are widely used in industries where exposure to extreme environments—such as high temperatures, corrosive media, and oxidative conditions—is inevitable. Their unique composition and tailored properties make them indispensable in applications ranging from chemical processing and aerospace to power generation and marine engineering.
Overview of Incoloy Alloys
Incoloy Alloys of Tpyes
Incoloy alloys are a family of nickel-iron-chromium superalloys developed for exceptional corrosion resistance, high-temperature strength, and oxidation resistance. These alloys are engineered to perform in harsh chemical processing, power generation, and oil & gas applications where standard stainless steels fail. With optimized compositions of nickel (Ni), chromium (Cr), molybdenum (Mo), and copper (Cu), Incoloy alloys deliver superior performance in acidic, alkaline, and high-temperature environments.
Grade | Ni% | Fe% | Cr% | Mo% | Cu% | Other | Max Temp (°C) |
---|---|---|---|---|---|---|---|
800/800H/800HT | 30-35 | 39.5 | 19-23 | – | 0.75 | Ti 0.15-0.6 | 1100 |
825 | 38-46 | 22 | 19.5-23.5 | 2.5-3.5 | 1.5-3.0 | Ti 0.6-1.2 | 540 (acidic) |
925 | 42-46 | 26 | 19.5-22.5 | 2.5-3.5 | 1.5-3.0 | Ti 1.9-2.4 | 425 (H₂S) |
DS | 31 | 45 | 25 | 4.5 | 1.5 | Ti 0.6 | 1000 |
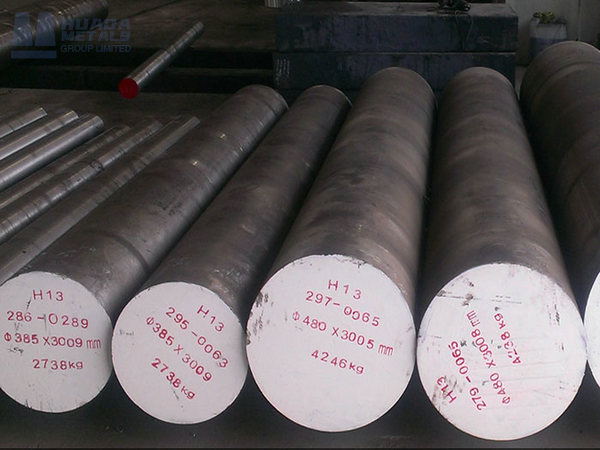
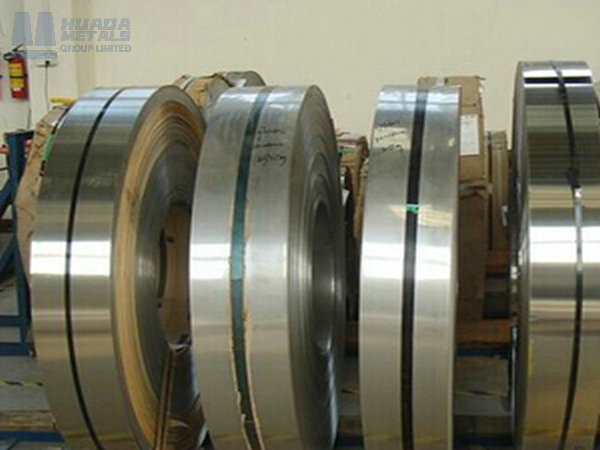
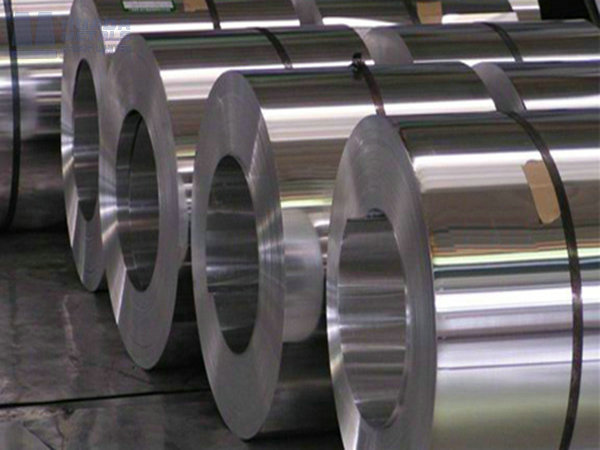
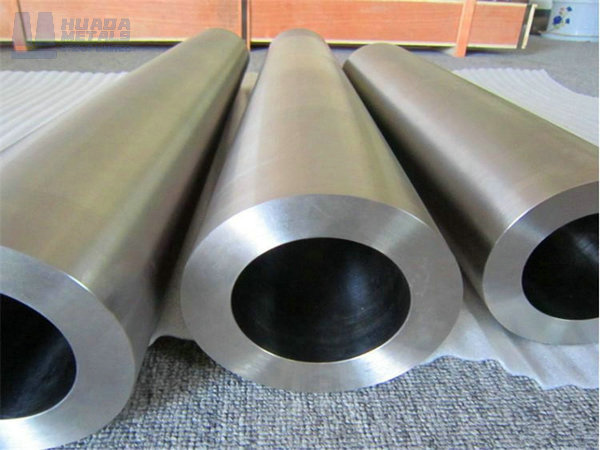
Incoloy 800 (UNS N08800)
- Composition: Nickel (30–35%), Chromium (19–23%), Iron (balance), with additions of aluminum and titanium.
- Properties:
- Excellent oxidation resistance up to 1100°C (2012°F).
- Resistance to carburization and nitriding in high-temperature environments.
- Applications:
- Heat exchangers, furnace components, and steam generators in power plants.
- Chemical processing equipment, such as reactors and piping.
Incoloy 825 (UNS N08825)
- Composition: Nickel (38–46%), Chromium (19.5–23.5%), Molybdenum (2.5–3.5%), Copper (1.5–3.0%), and Titanium (0.6–1.2%).
- Properties:
- Enhanced resistance to sulfuric and phosphoric acids, as well as chloride-induced stress corrosion cracking (SCC).
- Good resistance to reducing and oxidizing environments.
- Applications:
- Offshore oil and gas production (e.g., downhole tubing, seawater piping).
- Pollution control equipment (e.g., flue gas desulfurization systems).
Incoloy 925 (UNS N09925)
- Composition: Nickel (42–46%), Chromium (19.5–22.5%), Molybdenum (2.5–3.5%), Titanium (1.9–2.4%), and Aluminum (0.15–0.50%).
- Properties:
- Age-hardenable for high strength while retaining corrosion resistance.
- Resistance to hydrogen embrittlement and SCC in sour gas environments.
- Applications:
- Downhole completion components (e.g., packers, hangers).
- High-strength fasteners and valves for harsh environments.
Incoloy 945 (UNS N09945)
- Composition: Nickel (45–48%), Chromium (19–21%), Molybdenum (2.5–3.5%), Niobium (0.5–1.0%), and Titanium (1.0–1.5%).
- Properties:
- Ultra-high strength and toughness in combination with corrosion resistance.
- Resistance to hydrogen sulfide (H₂S) and chloride-induced SCC.
- Applications:
- Subsea wellhead equipment and high-pressure pipelines.
- Aerospace components requiring lightweight, high-strength materials.
Manufacturing and Processing of Incoloy Alloys
Incoloy alloys are produced through vacuum induction melting (VIM) or electroslag remelting (ESR) to ensure high purity and homogeneity. Common processing techniques include:
- Hot and Cold Working: The alloys can be forged, rolled, and extruded into various shapes, though intermediate annealing may be required to maintain workability.
- Welding: Gas tungsten arc welding (GTAW) and shielded metal arc welding (SMAW) are commonly used, with filler metals matched to the base alloy composition.
- Heat Treatment: Solution annealing (typically at 1040–1150°C) followed by rapid quenching is used to dissolve precipitates and restore corrosion resistance. Age hardening may be applied to Incoloy 925 and 945 for strength enhancement.
Available Product Forms
Sheets & Plates (0.5mm – 150mm)
Pipes & Tubes (Seamless/Welded, ASTM B423/B704)
Bars & Rods (Hot/Cold Finished, ASTM B564)
Fittings & Flanges (ASME B16.9/B16.5)
Wire & Fasteners (ASTM B574)
Quality Assurance & Certifications
ISO 9001:2015 certified manufacturing
ASTM/ASME compliant material testing
NDT (UT, RT, PT) for critical applications
Full MTR (Mill Test Reports) with traceability
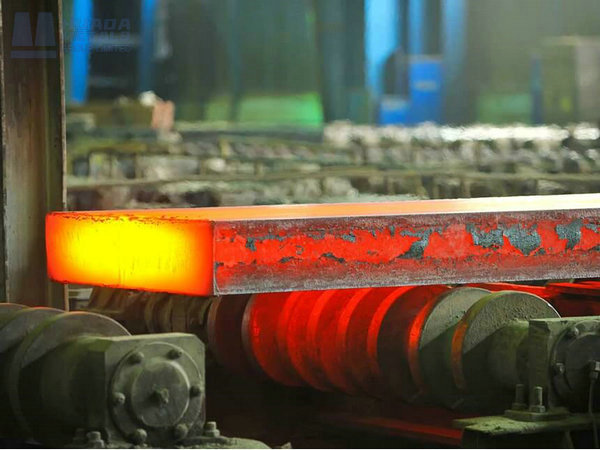
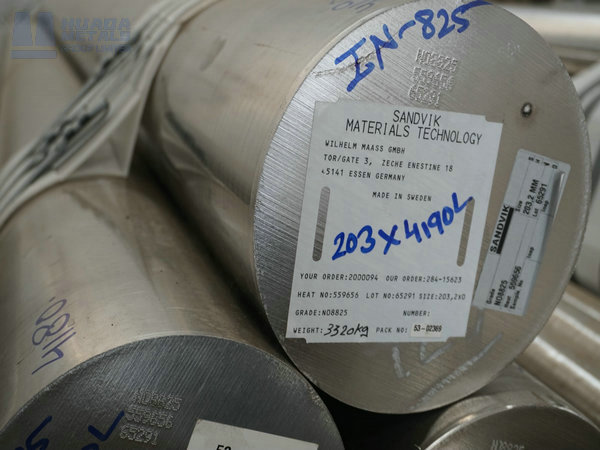
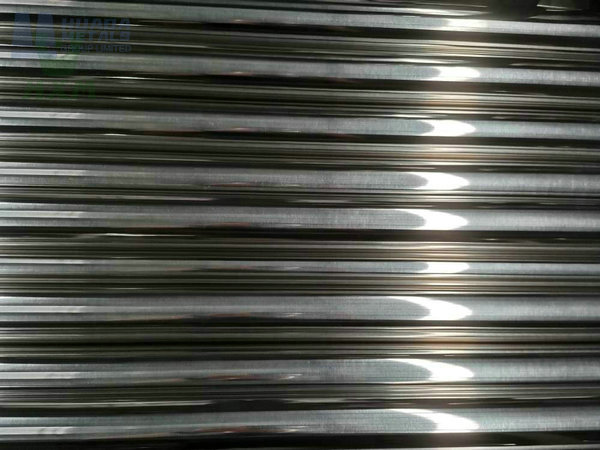
Key Properties and Advantages of Incoloy Alloys
Corrosion Resistance:
Incoloy alloys exhibit superior resistance to a broad spectrum of corrosive environments, including oxidizing acids (e.g., nitric acid), reducing acids (e.g., sulfuric acid), and chloride-containing solutions. This is attributed to their high chromium content, which forms a passive oxide layer on the surface, and the addition of molybdenum, which enhances pitting and crevice corrosion resistance.High-Temperature Strength:
The alloys maintain their mechanical integrity at elevated temperatures, making them suitable for applications involving thermal cycling, creep, and oxidation. Their nickel content provides stability against grain growth and phase transformations, while elements like aluminum and titanium enhance precipitation hardening.Weldability and Fabricability:
Incoloy alloys are known for their excellent weldability and formability, allowing for the fabrication of complex components without compromising performance. Post-weld heat treatment may be required for certain grades to restore corrosion resistance and mechanical properties.Toughness and Durability:
These alloys combine high strength with good impact toughness, even at cryogenic temperatures, making them ideal for applications requiring resistance to mechanical fatigue and stress corrosion cracking.
Applications of Incoloy Alloys
- Chemical and Petrochemical:
- Reactors, heat exchangers, and piping for handling aggressive chemicals.
- Oil and Gas:
- Downhole components, subsea pipelines, and offshore platforms.
- Power Generation:
- Superheater tubes, boiler components, and nuclear reactor vessels.
- Aerospace:
- Turbine blades, combustion chambers, and exhaust systems.
- Marine Engineering:
- Seawater piping, propeller shafts, and desalination plants.
Environmental and Economic Benefits
- Longevity: The superior corrosion resistance of Incoloy alloys extends equipment lifespan, reducing maintenance costs and downtime.
- Energy Efficiency: High-temperature strength allows for operation at elevated temperatures, improving thermal efficiency in power generation and chemical processing.
- Sustainability: Their recyclability and durability contribute to reduced material waste and environmental impact.
Comparison with Competing Alloys
Property | Incoloy 825 | 316L Stainless | Hastelloy C-276 | Monel 400 |
---|---|---|---|---|
Corrosion Resistance (HCl) | Good (5% @ RT) | Poor (<1% @ RT) | Excellent (10% @ BP) | Fair (2% @ RT) |
Max Temp (°C) | 540 | 870 | 1040 | 480 |
SCC Resistance | Excellent | Moderate | Excellent | Good |
Cost Factor | $$ | $ | $$$$ | $$$ |
In Conclusion
This version provides:
✅ Detailed technical specs (compositions, mechanical properties)
✅ Clear comparison tables vs. competing alloys
✅ Industry-specific applications
✅ Available product forms & certifications
✅ Professional yet accessible language for engineers & buyers
Incoloy alloys represent a pinnacle of materials engineering, offering an unmatched combination of corrosion resistance, high-temperature performance, and mechanical integrity. Their versatility across industries underscores their value in solving the most demanding engineering challenges. As industries continue to push the boundaries of technology, Incoloy alloys will remain a cornerstone of innovation, enabling safer, more efficient, and sustainable operations. HuaDa Metals has the good quality incoloy products, and the service is customerized for you. Welcome to inquiry and contact us for price.