Inconel alloys, a registered trademark of Special Metals Corporation, are a family of nickel-chromium-based superalloys renowned for their exceptional resistance to high temperatures, oxidation, corrosion, and mechanical stress. These alloys are engineered to maintain strength and structural integrity in environments where conventional materials fail, making them indispensable in aerospace, energy, chemical processing, and marine industries.
Inconel alloys are a premier family of nickel-chromium-based superalloys developed for exceptional performance in high-temperature, high-stress, and corrosive environments. These alloys combine oxidation resistance, mechanical strength, and fabricability, making them indispensable in aerospace, chemical processing, and energy applications where conventional materials fail.
Overview of Inconel Alloy
Inconel Alloy of Tpyes
Inconel 718 (UNS N07718)
- Composition:
- Nickel (50–55%)
- Chromium (17–21%)
- Niobium + Tantalum (4.75–5.5%)
- Molybdenum (2.8–3.3%)
- Titanium (0.65–1.15%)
- Aluminum (0.2–0.8%)
- Properties:
- Age-hardenable for ultra-high strength (tensile strength up to 1380 MPa).
- Applications:
- Aircraft engine components (turbine disks, blades, seals).
- Gas turbines, rocket motors, and nuclear reactors.
Inconel 625 (UNS N06625)
- Composition:
- Nickel (58% min.)
- Chromium (20–23%)
- Molybdenum (8–10%)
- Niobium (3.15–4.15%)
- Properties:
- Outstanding resistance to seawater, brine, and acidic environments.
- High strength without precipitation hardening.
- Applications:
- Marine engineering (propeller shafts, seawater piping).
- Chemical processing (heat exchangers, reactors).
- Aerospace ducting and exhaust systems.
Inconel 600 (UNS N06600)
- Composition:
- Nickel (72% min.)
- Chromium (14–17%)
- Iron (6–10%)
- Properties:
- Excellent resistance to high-temperature oxidation and carburization.
- Good corrosion resistance in reducing environments.
- Applications:
- Furnace components, heat-treating baskets.
- Nuclear reactor core components.
- Food processing equipment.
Inconel X-750 (UNS N07750)
- Composition:
- Nickel (70% min.)
- Chromium (14–17%)
- Titanium + Aluminum (2.25–2.75%)
- Properties:
- Spring-like properties after aging; retains strength at 800°C.
- Applications:
- Aircraft engine springs, fasteners, and turbine seals.
- Gas turbine blades and vanes.
- Oil and gas downhole tools (e.g., subsea wellhead components).
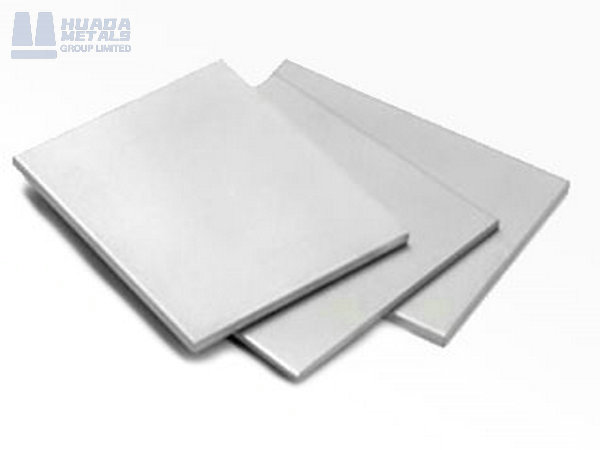
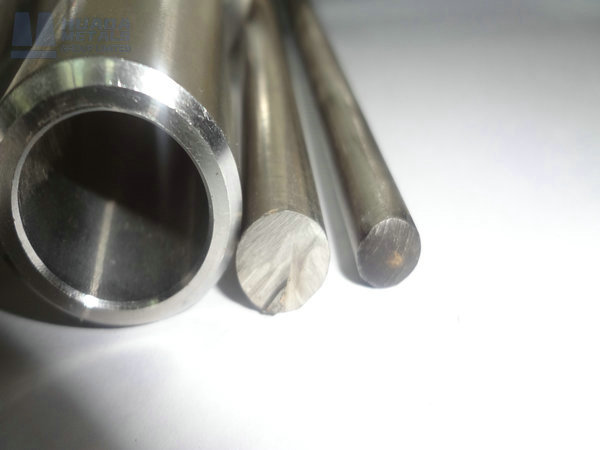
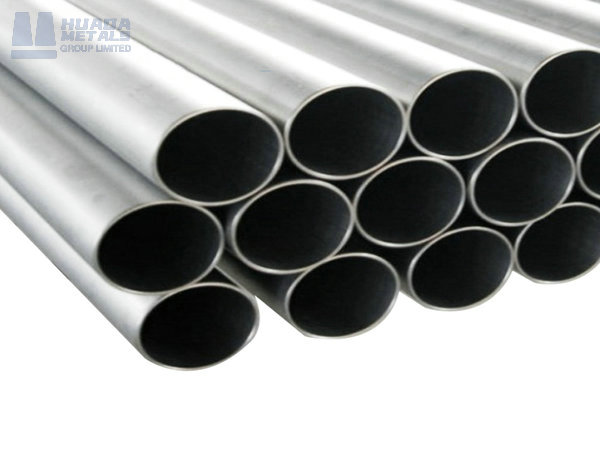
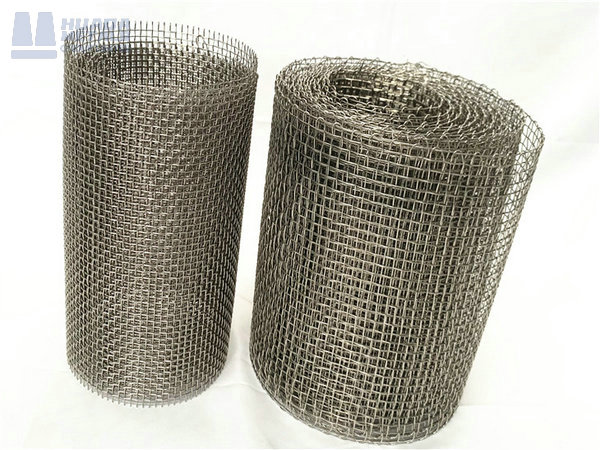
Inconel alloys, a premium family of nickel-chromium-based superalloys developed by Special Metals Corporation, are engineered to thrive in extreme environments where conventional materials fail. Renowned for their exceptional high-temperature strength (retaining integrity up to 700°C/1300°F and beyond), corrosion resistance (oxidizing, acidic, and chloride-rich media), and oxidation durability, Inconel alloys are indispensable in aerospace, energy, chemical processing, and marine industries.
Grade | Ni% | Cr% | Fe% | Mo% | Nb% | Other | Max Temp (°C) |
---|---|---|---|---|---|---|---|
600 | ≥72 | 14-17 | 6-10 | – | – | Cu 0.5 | 1150 |
625 | ≥58 | 20-23 | ≤5 | 8-10 | 3.15-4.15 | Co 1.0 | 980 |
718 | 50-55 | 17-21 | Bal. | 2.8-3.3 | 4.75-5.5 | Ti 0.65-1.15 | 700 |
X-750 | ≥70 | 14-17 | 5-9 | – | 0.7-1.2 | Al 0.4-1.0 | 870 |
HX | 47 | 22 | 18 | 9 | – | Co 1.5, W 0.6 | 1200 |
Available Product Forms
Sheets/Plates (0.1mm – 300mm)
Pipes/Tubes (Seamless: ASTM B444; Welded: B704)
Bars/Rods (Hot/Cold Finished: ASTM B637)
Forgings (AMS 5662/5663 for aerospace)
Wire (AWS A5.14 for welding)
Quality Assurance
AMS/Nadcap certified for aerospace
NDT Testing: UT, RT, PT per ASTM E1417
Full Traceability: Mill test reports (MTR) with heat/lot numbers
- ISO Certifications and the SCS Certification Book.
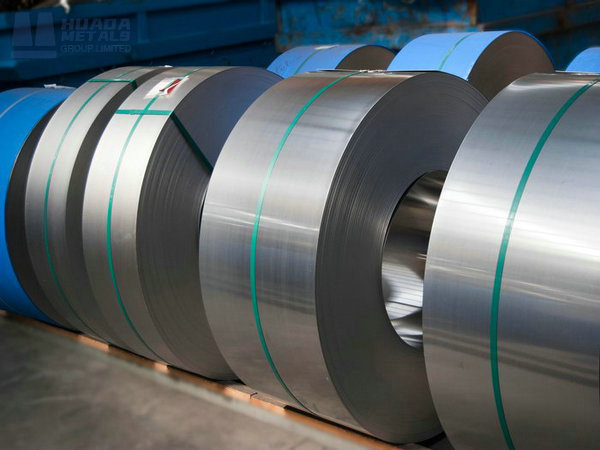
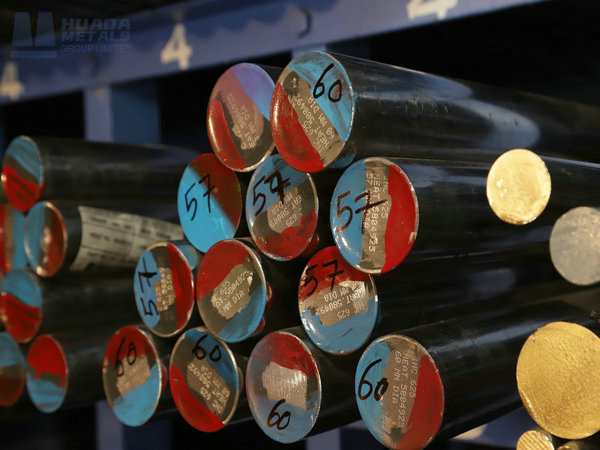
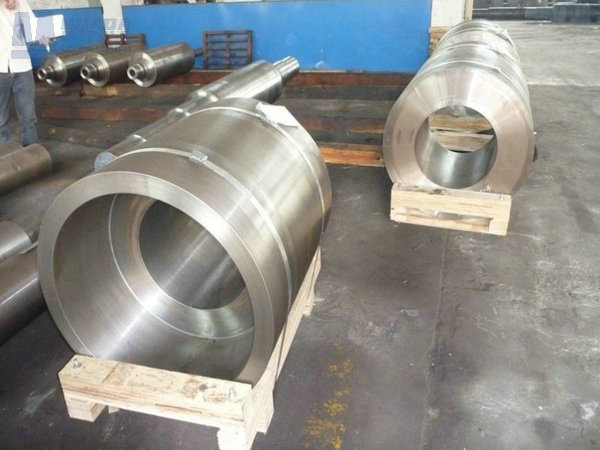
Key Properties and Advantages of Inconel Alloy
- High-Temperature Strength:
Inconel alloys retain their mechanical properties at elevated temperatures (up to 700°C/1300°F and beyond) due to their unique precipitation-hardening mechanisms, which involve the formation of γ’ (Ni₃(Al,Ti)) and γ” (Ni₃Nb) phases. - Corrosion Resistance:
The high chromium content (15–23%) provides superior resistance to oxidizing environments, while additions of molybdenum, niobium, and titanium enhance resistance to pitting, crevice corrosion, and stress corrosion cracking (SCC) in chloride-rich and acidic media. - Oxidation and Carburization Resistance:
A stable, adherent oxide layer forms on the surface, protecting the alloy from scaling and carburization in high-temperature thermal cycling conditions. - Weldability and Fabricability:
Inconel alloys are highly weldable using techniques like TIG, MIG, and electron beam welding. Specialized filler metals (e.g., ERNiCrFe-7) ensure seam integrity in critical applications. - Fatigue and Creep Resistance:
Their microstructure resists grain growth and phase transformations, making them ideal for long-term service under cyclic loading and creep conditions.
Manufacturing and Processing
- Melting Practices:
Inconel alloys are produced via vacuum induction melting (VIM) followed by electroslag remelting (ESR) or vacuum arc remelting (VAR) to ensure purity and homogeneity. - Forming and Machining:
- Hot working (forging, rolling) is performed at 980–1200°C.
- Cold working requires careful tooling due to work hardening; carbide or ceramic tools are recommended.
- Machinability improves in the solution-annealed condition.
- Heat Treatment:
- Solution Annealing: 980–1040°C, followed by rapid quenching.
- Precipitation Hardening (Aging):
- For 718: 720°C for 8 hours, furnace cool to 620°C, hold for 8 hours.
- For X-750: 730°C for 16 hours, air cool.
- Welding:
- Preheat and post-weld heat treatment may be required to avoid cracking.
- Pulsed gas tungsten arc welding (GTAW-P) is preferred for thin sections.
Applications of Inconel Alloy
- Aerospace:
- Turbine blades, combustors, and exhaust systems.
- Fasteners, springs, and landing gear components.
- Oil and Gas:
- Subsea wellheads, downhole completion tools, and umbilicals.
- Flare stacks and heat exchangers in sour gas (H₂S) environments.
- Power Generation:
- Gas turbine blades, boiler tubes, and nuclear reactor internals.
- Chemical Processing:
- Reactors, distillation columns, and pollution control equipment (e.g., flue gas desulfurization systems).
- Marine:
- Seawater valves, pumps, and offshore platforms.
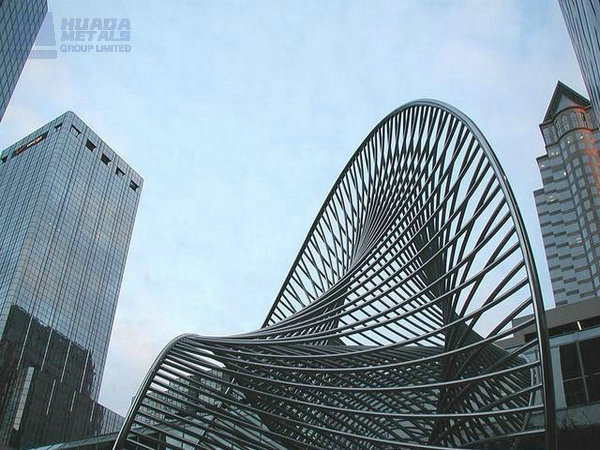
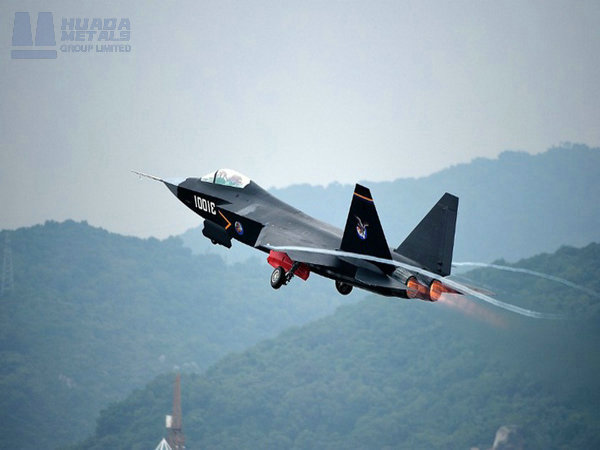
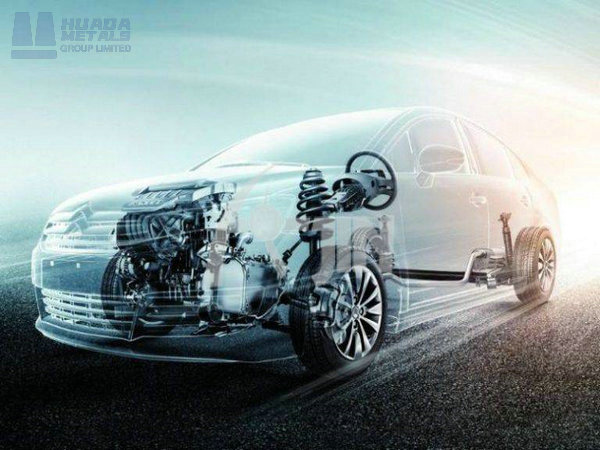
Environmental and Economic Advantages
- Longevity:
Inconel alloys extend equipment lifespan, reducing downtime and maintenance costs. - Energy Efficiency:
Their high-temperature strength allows for higher operating temperatures, improving thermal efficiency. - Sustainability:
Recyclable and durable, Inconel alloys minimize material waste and environmental impact.
Comparison with Competing Alloys
Property | Inconel 718 | Stainless 316L | Hastelloy C-276 | Titanium Gr5 |
---|---|---|---|---|
Max Temp (°C) | 700 | 870 | 1040 | 600 |
Yield Strength (MPa) | 1030 | 170 | 350 | 828 |
Corrosion Resistance | Good (oxidizing) | Moderate | Excellent (reducing) | Excellent (chlorides) |
Cost Factor | $$$ | $ | $$$$ | $$ |
In Conclusion
Inconel alloys represent the pinnacle of high-performance materials, offering unmatched reliability in extreme conditions. Their versatility across industries—from deep-sea drilling to hypersonic flight—makes them a cornerstone of modern engineering. As industries demand ever-higher performance, Inconel alloys continue to evolve, ensuring they remain at the forefront of innovation. HuaDa Metals has the good quality inconel alloys and contact us.
Inconel alloys occupy a critical niche in modern engineering by enabling industries to operate safely and efficiently in environments where conventional materials rapidly degrade. As nickel-chromium-based superalloys, they combine high-temperature resilience, corrosion immunity, and mechanical toughness to address challenges spanning aerospace, energy, oil and gas, and marine sectors. Their ability to retain strength above 700°C (1300°F) while resisting oxidation, carburization, and thermal fatigue makes them indispensable for gas turbine engines, rocket propulsion systems, and nuclear reactors, where component failure could have catastrophic consequences. The alloy’s weldability and formability further allow its integration into complex, mission-critical components, from aircraft turbine blades to deep-sea exploration tools.