Austenitic stainless steels (ASS) are the most widely used category of stainless steels, renowned for their exceptional corrosion resistance, formability, and mechanical properties. Characterized by a face-centered cubic (FCC) crystal structure, these alloys contain significant chromium (Cr), nickel (Ni), and nitrogen (N) contents, which stabilize the austenitic phase at room temperature. This composition ensures superior ductility, toughness, and resistance to localized corrosion, making ASS indispensable in industries ranging from chemical processing to biomedical engineering.
- Chemical processing: Pressure vessels, heat exchangers (304/316L).
- Oil and gas: Subsea pipelines, offshore platforms (duplex 2205 for chloride resistance).
- Aerospace: Engine components, fasteners (high-Ni grades like 347).
- Nuclear energy: Reactor internals, fuel cladding (316LN for neutron irradiation tolerance).
Specification and Properties of Austenitic Stainless Steels
The austenitic phase remains stable even at cryogenic temperatures due to the high stacking fault energy (SFE) induced by Ni and N. This contrasts with ferritic or martensitic stainless steels, which undergo phase transformations under similar conditions.
The defining chemical features of austenitic stainless steels include:
- Chromium (Cr): 16–26 wt% – Forms a passive oxide layer (Cr₂O₃) that shields the steel from aggressive environments.
- Nickel (Ni): 8–22 wt% – Stabilizes the austenitic phase, enhancing ductility and corrosion resistance.
- Nitrogen (N): 0.05–0.25 wt% (in high-nitrogen variants) – Increases strength, work hardening rate, and pitting resistance.
- Molybdenum (Mo): 2–3 wt% (in grades like 316/316L) – Improves resistance to chloride-induced pitting and crevice corrosion.
- Manganese (Mn): Up to 12 wt% (in low-Ni grades) – Acts as a partial Ni substitute, stabilizing austenite while reducing costs.
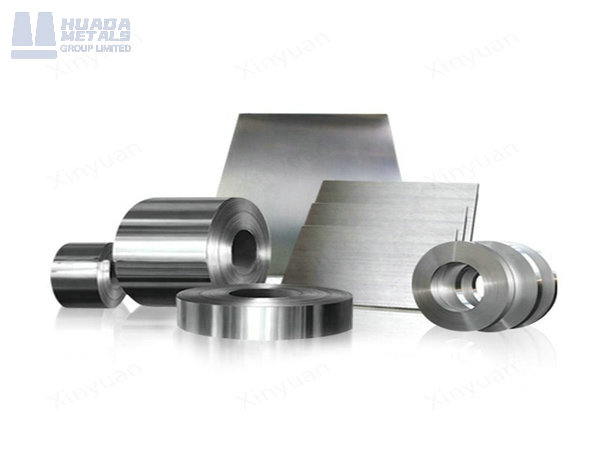
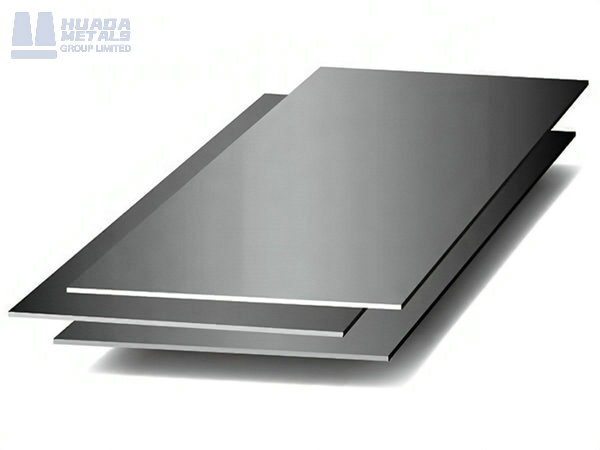
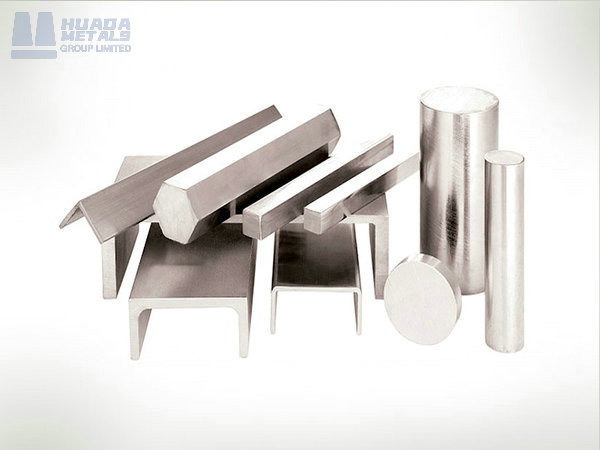
Chemical Composition of Austenitic Stainless Steels
Grade | UNS | Cr% | Ni% | C% | Mo% | Other | PREN¹ |
---|---|---|---|---|---|---|---|
304 | S30400 | 18-20 | 8-10.5 | ≤0.08 | – | – | 19 |
304L | S30403 | 18-20 | 8-12 | ≤0.03 | – | – | 19 |
316 | S31600 | 16-18 | 10-14 | ≤0.08 | 2-3 | – | 26 |
316L | S31603 | 16-18 | 10-14 | ≤0.03 | 2-3 | – | 26 |
317L | S31703 | 18-20 | 11-15 | ≤0.03 | 3-4 | – | 32 |
904L | N08904 | 19-23 | 23-28 | ≤0.02 | 4-5 | Cu 1-2 | 36 |
254 SMO® | S31254 | 19.5-20.5 | 17.5-18.5 | ≤0.02 | 6-6.5 | N 0.18-0.22 | 43 |
Physical Properties of Austenitic Stainless Steel
Property | 304 | 316 | 904L |
---|---|---|---|
Density (g/cm³) | 8.00 | 8.03 | 8.24 |
Melting Range (°C) | 1400-1450 | 1375-1400 | 1350-1400 |
Thermal Conductivity (W/m·K) | 16.2 | 15.9 | 12.5 |
Electrical Resistivity (μΩ·m) | 0.72 | 0.74 | 0.85 |
CTE (20-100°C, μm/m·°C) | 17.2 | 16.5 | 15.0 |
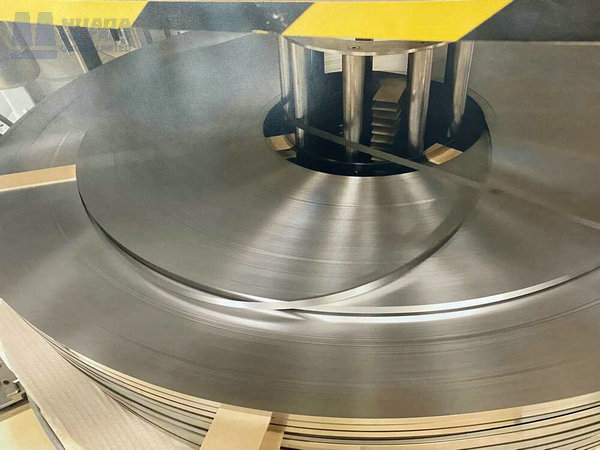
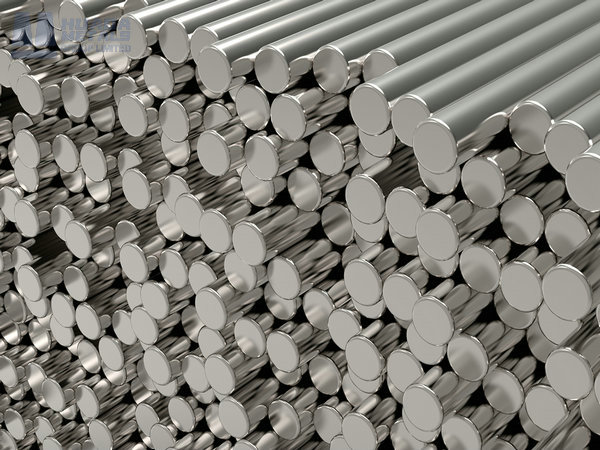
Mechanical Properties of Austenitic Stainless Steel
Grade | YS (MPa) | UTS (MPa) | Elongation (%) | Hardness (HB) |
---|---|---|---|---|
304 | 205 | 515 | 40 | 201 |
316 | 205 | 515 | 40 | 217 |
316L | 170 | 485 | 40 | 217 |
904L | 220 | 490 | 35 | 230 |
254 SMO | 300 | 650 | 35 | 290 |
Metallurgical Advantages of Austenitic Stainless Steel
- Corrosion Resistance
The passive chromium oxide layer provides immunity to:
- Atmospheric corrosion: Suitable for outdoor architectural components (e.g., 304 stainless steel in building cladding).
- Chemical environments: Resists acids, alkalis, and salts (e.g., 316L in pharmaceutical reactors).
- Localized corrosion: Nitrogen-enhanced grades (e.g., 316Ti) withstand pitting in chloride-rich media (e.g., seawater pipelines).
- High-Temperature Performance
- Oxidation resistance: Up to 1,000°C (e.g., 310S in furnace linings).
- Creep resistance: Stabilized by titanium (Ti) or niobium (Nb) additions (e.g., 321 in exhaust systems).
- Biocompatibility
Medical implants: 316LVM (low carbon, vacuum-melted) meets ASTM F138 standards for orthopedic screws and dental prostheses.
- Cryogenic Applications
LNG storage: 304L and 316L retain ductility at −196°C, critical for preventing brittle fracture.
- Key Industries
- Chemical processing: Pressure vessels, heat exchangers (304/316L).
- Oil and gas: Subsea pipelines, offshore platforms (duplex 2205 for chloride resistance).
- Aerospace: Engine components, fasteners (high-Ni grades like 347).
- Nuclear energy: Reactor internals, fuel cladding (316LN for neutron irradiation tolerance).
Manufacturing Considerations of Austenitic Stainless Steel
Production Processes of Austenitic Stainless Steel
Hot Rolling: 1150-1260°C for plates/bars (ASTM A240/A276)
Cold Rolling: Achieves mirror finishes (BA/2B/No.4)
Welding:
GTAW/GMAW with 308L/316L filler
Post-weld annealing (1040-1120°C) for critical applications
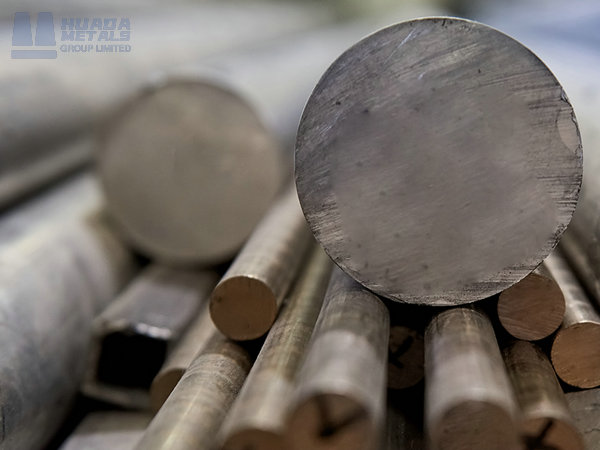

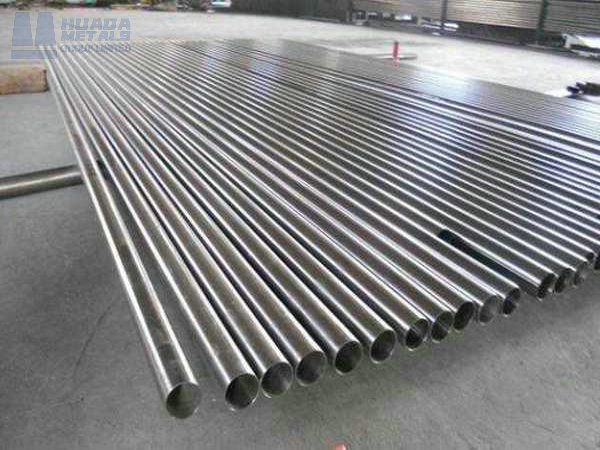
Cost Drivers of Austenitic Stainless Steel
- Cost Drivers
- Nickel price volatility: Accounts for 30–50% of raw material costs (impacting 304/316L pricing).
- Nitrogen addition: High-pressure sintering (e.g., metal injection molding, MIM) increases production costs but reduces Ni dependency.
- Surface finishing: Electropolishing (for medical devices) or passivation (for food-grade applications) adds 10–15% to costs.
- Key Manufacturing Routes
- Hot/Cold Rolling: Produces sheets, tubes, and wires (304/316L).
- Additive Manufacturing (AM): Selective laser melting (SLM) of 17-4PH (pre-hardened martensitic grade) or 316L (for complex geometries).
- Powder Metallurgy (PM): High-nitrogen grades (e.g., P2000) via nitrogen absorption during sintering.
- Heat Treatment Considerations
- Solution annealing: 1,050–1,150°C (for recrystallization and corrosion resistance).
- Cryogenic treatment: −196°C (to transform retained austenite into martensite, improving wear resistance in tools).
Industry Applications of Austenitic Stainless Steel
Chemical Processing
304: Storage tanks for nitric acid
316L: Heat exchangers for sulfuric acid
254 SMO: Seawater piping systems
Food & Pharmaceutical
316L: Bioreactors, CIP/SIP systems
Electropolished 304: Dairy processing lines
Architecture
304: Structural façades (6-8mm thickness)
316: Coastal building components
Medical
317LVM: Implant-grade material (ASTM F138)
304: Surgical instrument bodies
Comprehensive Table of Industry Applications
Industry | Key Applications | Preferred Grades | Critical Properties Required | Competing Materials | Why Austenitic Wins? |
---|---|---|---|---|---|
Chemical Processing | Reactors, heat exchangers, piping | 316L, 317L, 904L, 254 SMO | Chloride resistance, pitting/crevice corrosion immunity | Duplex 2205, Nickel alloys | Lower cost than Ni alloys, better fabricability than duplex |
Food & Beverage | Tanks, conveyors, processing lines | 304, 316L (Electropolished) | Hygienic surface (Ra <0.8µm), cleanability | Plastics, Aluminum | Non-porous, sterilizable, no leaching |
Pharmaceutical | Bioreactors, CIP/SIP systems | 316L, 316LVM | Ultra-low carbon (≤0.03%), passivation compliance | Titanium, Glass-lined steel | Cost-effective, weldable, inert |
Oil & Gas | Subsea pipelines, valves | 316L, 254 SMO | H₂S/CO₂ resistance (NACE MR0175) | Super duplex, Inconel | Balanced cost vs. performance |
Architecture | Facades, railings, roofing | 304, 316 | Aesthetic finish (No.4, BA), atmospheric corrosion resistance | Corten steel, Aluminum | No maintenance, superior longevity |
Medical | Implants, surgical tools | 316LVM, 304 | Biocompatibility (ISO 5832-1), fatigue resistance | Titanium, Co-Cr alloys | Lower cost, easier machining |
Energy | Nuclear piping, flue gas scrubbers | 304H, 316Ti | High-temp strength (up to 800°C) | Incoloy, Ferritic steels | Oxidation resistance, thermal stability |
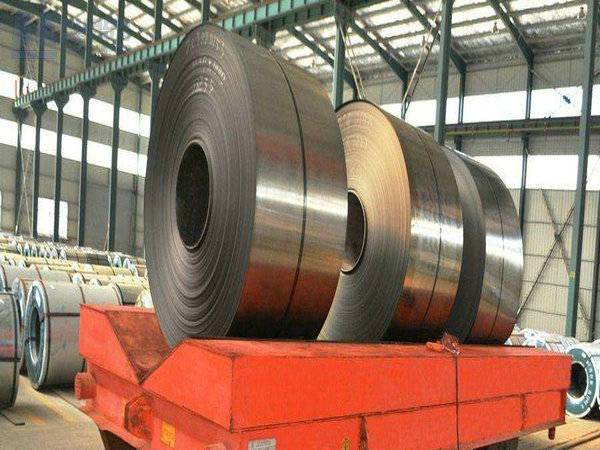
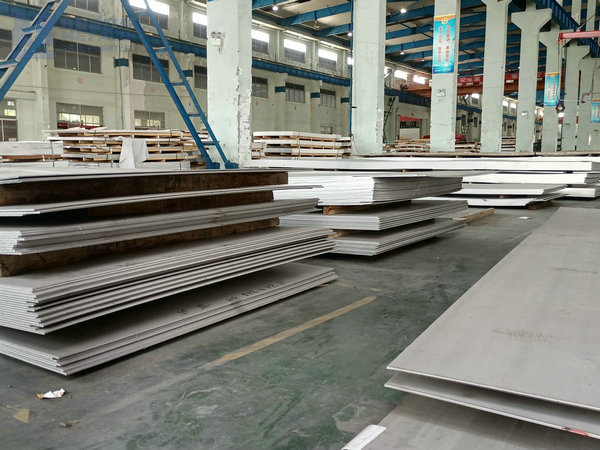
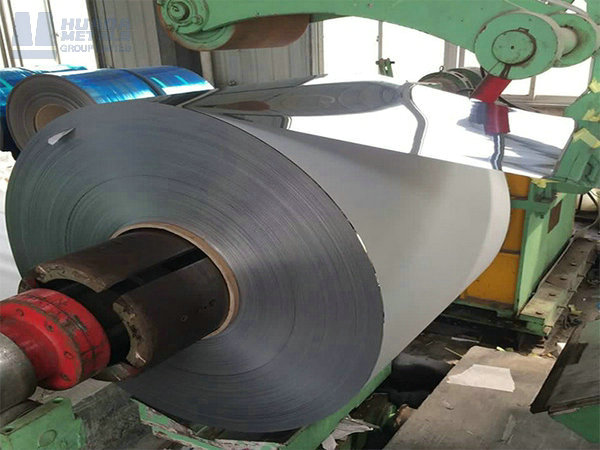
Austenitic Stainless Steel Vs Other Metals
Whether specified for pharmaceutical cleanrooms, chemical reactors, or iconic architectural structures, austenitic steels continue to dominate applications where reliability, cleanliness, and structural integrity are non-negotiable. Their compatibility with all modern fabrication techniques – from precision welding to deep drawing – ensures continued relevance in evolving industrial landscapes.
Quality Standards
ASTM A240: Pressure vessel plates
ASTM A312: Seamless/welded pipes
EN 10088-2: European structural standard
ASME SA-479: Machined components
Technical Support Services
Corrosion testing per ASTM G48/G150
Weld procedure qualification (PQR/WPS)
Material selection optimization
Competitive Positioning vs. Alternative Materials
Scenario | Austenitic Choice | Next-Best Alternative | Cost Ratio | Performance Delta |
---|---|---|---|---|
Seawater heat exchanger | 254 SMO | Super Duplex 2507 | 1:1.2 | +15% PREN, better weldability |
Pharma bioreactor | 316L Electropolished | Titanium Gr2 | 1:5 | -5% corrosion resistance, +300% cost savings |
Architectural cladding | 304 (2B finish) | Aluminum 5052 | 1:1.5 | No weathering discoloration |
In Conclusion
Austenitic stainless steels represent the gold standard for corrosion-resistant engineering materials, combining exceptional durability with unmatched versatility. Their face-centered cubic structure, stabilized by 8-12% nickel content, delivers unique advantages including cryogenic-to-elevated temperature performance, innate corrosion resistance, and superior formability. From food-safe 316L with electropolished finishes to ultra-resistant 6% Mo grades for seawater service, these alloys solve critical material challenges across industries. While higher in initial cost than carbon steels, their zero-maintenance longevity, full recyclability, and hygienic properties deliver superior lifecycle value. The addition of molybdenum (316 series) and nitrogen (super austenitics) extends performance in aggressive environments, often eliminating the need for expensive nickel alloys.
Austenitic stainless steels represent a cornerstone of modern engineering materials, offering an unparalleled balance of corrosion resistance, mechanical performance, and versatility. While their cost sensitivity to nickel markets and susceptibility to chloride-induced pitting in marginal environments remain challenges, advancements in nitrogen alloying and additive manufacturing continue to expand their applications. From medical implants to nuclear reactors, ASS remains the alloy of choice for industries demanding reliability under extreme conditions.Welcome to contact us HuaDa Metals.