Medium carbon steels, with carbon content ranging from 0.30% to 0.60%, occupy a critical position between low-carbon and high-carbon steels. These alloys deliver enhanced strength and hardness while maintaining reasonable ductility, making them ideal for high-stress mechanical components. The controlled addition of manganese (0.60-1.65%) and optional microalloying elements (Cr, Ni, Mo) enables tailored performance for demanding applications.
Medium carbon steel stands as a versatile and widely used category of ferrous alloys, finding its place across numerous industrial applications due to its balanced mechanical properties. Comprising carbon content typically ranging from 0.25% to 0.60% by weight, this type of steel offers a unique combination of strength, ductility, and toughness, making it a preferred choice for various engineering components.
Overview of Medium Carbon Steel
The defining characteristic of medium carbon steel is its carbon content, which significantly influences its properties. In addition to carbon, small amounts of other elements such as manganese (Mn), silicon (Si), sulfur (S), and phosphorus (P) are also present. Manganese is added to enhance hardenability and strength, while silicon acts as a deoxidizer. Sulfur and phosphorus are generally considered impurities, with their levels carefully controlled to avoid detrimental effects on the steel’s ductility and toughness.
Chemical Composition of Medium Carbon Steel
Grade | C% | Mn% | Si% | Cr% | Other | Equivalent Standards |
---|---|---|---|---|---|---|
AISI 1035 | 0.32-0.38 | 0.60-0.90 | 0.15-0.35 | – | – | ASTM A29, JIS S35C |
AISI 1045 | 0.43-0.50 | 0.60-0.90 | 0.15-0.35 | – | – | DIN C45, GB 45# |
AISI 4140 | 0.38-0.43 | 0.75-1.00 | 0.15-0.35 | 0.80-1.10 | Mo 0.15-0.25 | AMS 6349, EN 42CrMo4 |
AISI 4340 | 0.38-0.43 | 0.60-0.80 | 0.15-0.35 | 0.70-0.90 | Ni 1.65-2.00, Mo 0.20-0.30 | AMS 6414, EN 1.6565 |

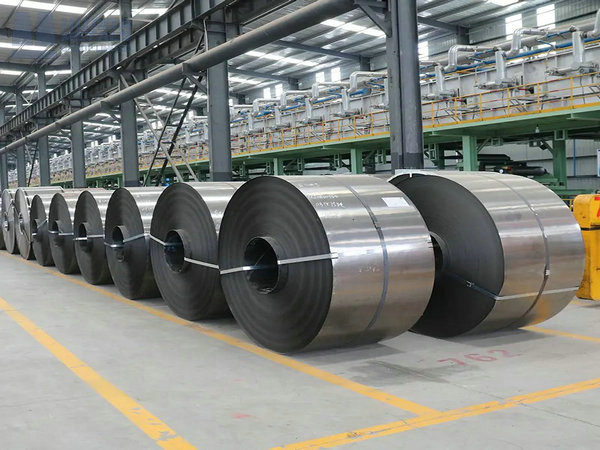
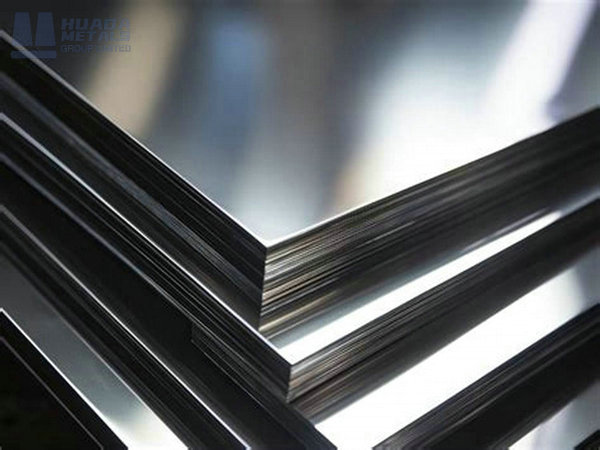
Physical & Mechanical Properties of Medium Carbon Steel
Property | Value Range |
---|---|
Density | 7.85 g/cm³ |
Melting Point | 1420-1540°C |
Thermal Conductivity | 42-50 W/m·K |
Electrical Conductivity | 8-12% IACS |
Coefficient of Thermal Expansion | 11.5-12.5 µm/m·°C |
Grade | Condition | Tensile Strength (MPa) | Yield Strength (MPa) | Elongation (%) | Hardness (HB) |
---|---|---|---|---|---|
1045 | Annealed | 585 | 450 | 12 | 170 |
1045 | Quenched & Tempered | 850 | 650 | 10 | 250 |
4140 | Annealed | 655 | 415 | 25 | 197 |
4140 | Q&T (540°C) | 1020 | 850 | 18 | 302 |
4340 | Q&T (425°C) | 1275 | 1170 | 12 | 388 |
Key Advantages of Medium Carbon Steel
- Cost-Effectiveness: Medium carbon steel offers a good balance of performance and cost compared to high-alloy steels, making it an economical choice for many applications.
- Versatility: Through heat treatment, its mechanical properties can be adjusted to meet the specific requirements of different applications, providing flexibility in design and manufacturing.
- Weldability: It generally exhibits better weldability compared to high carbon steels, facilitating the fabrication of complex structures.
- Availability: Medium carbon steel is readily available in various forms, such as bars, plates, sheets, and forgings, from steel suppliers worldwide.
HuaDa Metals has the various shape of the carbon steel content: 0.25%-0.60% Properties: Increased strength and hardness, decreased ductility and toughness, preheating for welding. Applications: Gears, shaft parts, machine tool guides. Examples: 45 steel (carbon content 0.42%-0.50.
✔ Optimized Strength-Ductility Balance
50-100% stronger than low carbon steels while maintaining 10-20% elongation
Fatigue strength up to 500 MPa (10⁷ cycles) for rotating components
✔ Heat Treatment Versatility
Through-hardening capability (up to 60mm section thickness)
Surface hardening options (induction/case hardening for wear resistance)
✔ Machining Performance
Free-machining variants (1144 stress-proof) achieve 80% machinability rating
Superior chip formation vs. high-carbon steels
✔ Cost Efficiency
30-50% lower cost than alloy steels for equivalent strength levels
Reduced machining time due to optimal hardness (200-300 HB)
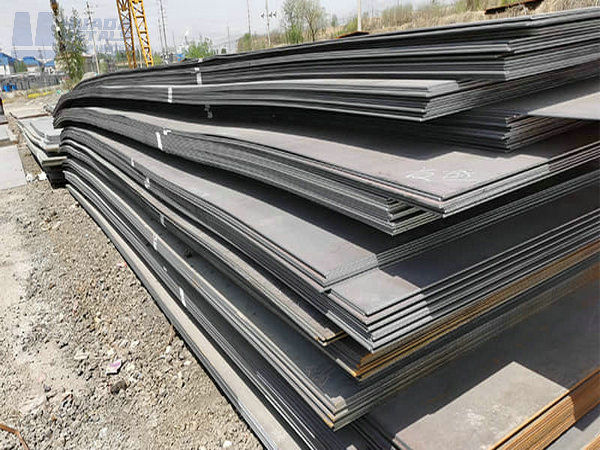
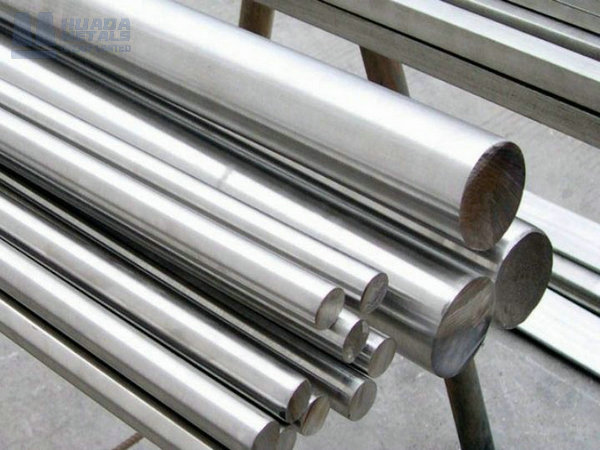
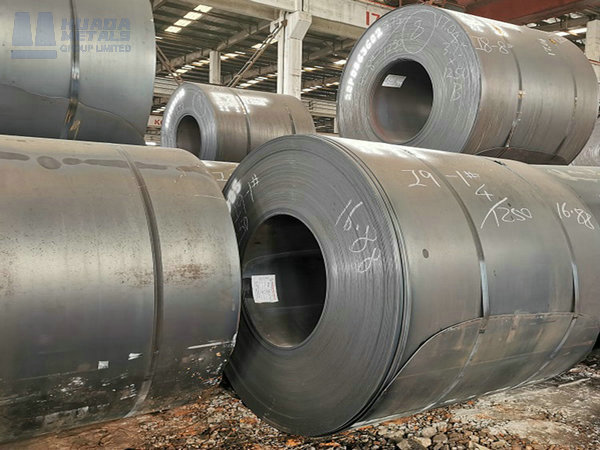
At the microstructural level, medium carbon steel in its annealed state consists of a ferrite-pearlite matrix. Ferrite, a soft and ductile phase, provides the steel with good formability, while pearlite, a lamellar mixture of ferrite and cementite (Fe₃C), imparts strength and hardness. The relative proportions of ferrite and pearlite depend on the carbon content and the cooling rate during solidification. As the carbon content increases, the volume fraction of pearlite rises, leading to higher strength and hardness but a slight reduction in ductility.
Manufacturing Processes of Medium Carbon Steel
Quenching involves rapidly cooling the steel from its austenitizing temperature, typically in water or oil, to transform the microstructure into martensite, a hard and brittle phase. This process significantly increases the steel’s hardness and strength but also makes it more prone to cracking and reduced toughness. To mitigate these issues, tempering is performed after quenching. Tempering entails reheating the quenched steel to a temperature below the critical point and holding it for a specific time, followed by air cooling. This process reduces the hardness of martensite slightly while improving the steel’s toughness and ductility, resulting in a more balanced set of mechanical properties.
Primary Production Routes
- Electric Arc Furnace (EAF) Recycling:
- Dominates medium carbon steel production (70% market share) due to lower capital costs (150/tonvs.250/ton for BOF).
- Cost: 0.8–1.0/kg (includes scrap, energy, and alloys).
- Basic Oxygen Furnace (BOF) Steelmaking:
- Preferred for high-volume production (e.g., 1 million tons/year at Nippon Steel’s Kimitsu plant).
- Cost: 0.7–0.9/kg (with iron ore and coke inputs).
- Hot Forging:
- 1045 steel billets forged at 1,100–1,200°C into crankshafts (die life: 5,000–8,000 cycles with TiN coating).
- Cost Drivers: Die wear (10,000–20,000 per set) and energy (1.2 kWh/kg forging energy).
- Cold Drawing:
- 5140 steel wires drawn to ±0.005 mm tolerance for precision springs (surface finish: Ra 0.2 μm via polishing).
- Energy Efficiency: 95% reduction in cross-sectional area with 25% elongation.
Cost Breakdown (5160 Steel Spring, 25 mm Dia.)
The mechanical properties of medium carbon steel can be tailored through heat treatment processes such as annealing, normalizing, quenching, and tempering. In its as-rolled or normalized condition, medium carbon steel exhibits moderate strength and good ductility, making it suitable for applications that require both formability and load-bearing capacity.
Component | Cost Contribution (%) | Optimization Levers |
---|---|---|
Raw Material | 55–65 | Use of EAF scrap reduces input cost by 30% vs. BOF iron ore. |
Heat Treatment | 20–25 | Induction hardening (0.15/kg)vs.furnacehardening(0.25/kg) for batch sizes >1,000. |
Machining | 10–15 | Near-net-shape forging reduces CNC time by 60%. |
Coating | 5–10 | Zinc-nickel plating (1.5/kg)vs.manganesephosphate(0.6/kg) for corrosion resistance. |
Applications of Medium Carbon Steel
The tensile strength of medium carbon steel typically ranges from 600 to 800 MPa (87 to 116 ksi), with yield strengths in the range of 350 to 550 MPa (51 to 80 ksi). The elongation at fracture, a measure of ductility, can vary from 10% to 25%, depending on the heat treatment and carbon content.
The combination of strength, ductility, and weldability makes medium carbon steel suitable for a wide range of applications across various industries:
Automotive
Powertrain: Crankshafts (1045 forged), axle shafts (4140)
Suspension: Steering knuckles, torsion bars
Heavy Machinery
Construction: Hydraulic cylinder rods (1045 chrome-plated)
Mining: Dragline bucket pins (4340 Q&T)
Industrial Equipment
Tooling: Jigs/fixtures (1144 stress-proof)
Fluid Systems: High-pressure fittings (4130)
Defense/Aerospace
Landing gear components (4340, AMS-S-5000)
Armor plate (hardened 4340 at 500BHN)
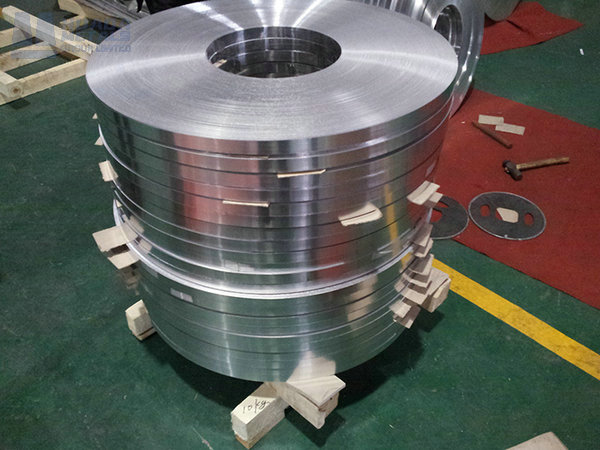
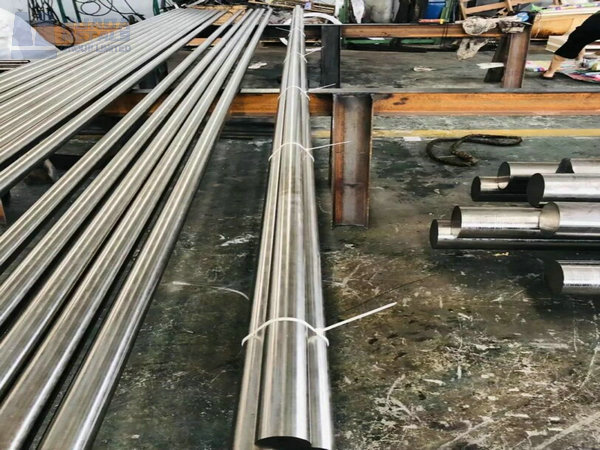
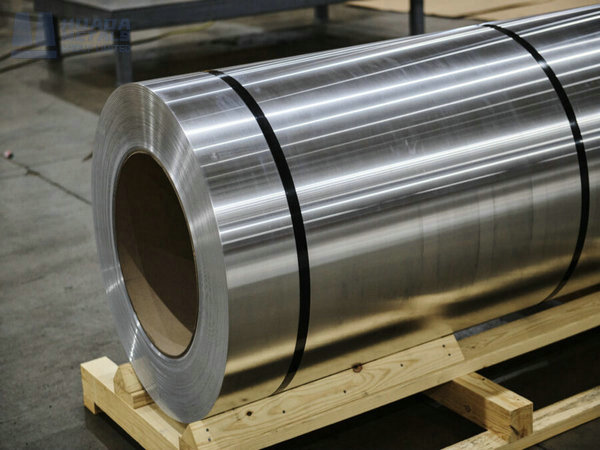
Production Methods
- Hot Forging: 1100-1250°C working temperature for crankshafts/gears
Precision Machining: CNC turning/milling of heat-treated blanks
Heat Treatment:
Quench & Temper (oil/water quenching + 200-650°C tempering)
Normalizing (air cooling from 870°C for uniform microstructure)
Cost Structure
Process | Cost Factor | Impact on Properties |
---|---|---|
Hot-rolled bar stock | $ | As-rolled properties (σₓ=500-600MPa) |
Cold-drawn precision bar | $$ | +15% strength, tighter tolerances (±0.05mm) |
Q&T heat treatment | $$$ | 2-3X strength increase |
Surface hardening | $$$$ | Wear resistance (HRC 50-60 case depth) |
Medium Carbon Steel
Quality Standards
ASTM A322: Standard for alloy steel bars
AMS 2759/1: Aerospace heat treatment requirements
ISO 683-1: Heat-treatable steel specifications
Technical Support Services
Microstructure analysis (per ASTM E3/E407)
Hardness profile mapping for case-hardened parts
Fatigue life prediction using FEA modeling
Medium carbon steel is a fundamental material in the engineering world, valued for its well-rounded properties and adaptability. Its ability to be processed and heat-treated to achieve a wide range of mechanical characteristics makes it indispensable in countless industrial applications, despite facing some limitations in certain extreme conditions. As technology advances and new alloying and processing techniques emerge, the role of medium carbon steel continues to evolve, ensuring its relevance in modern manufacturing and construction.
In Conclusion
HuaDa Metals has the good quality products in medium carbon steel, and the service is customerized for every clients, please contact us or ask for the lastest price. This technical profile provides: Grade-specific property data for engineering calculations, Heat treatment, optimization guidance, Cost-performance tradeoff analysis , Application-based selection methodology.
Medium carbon steels remain indispensable for high-stress, high-wear applications, offering optimized strength, toughness, and machinability through tailored alloying and heat treatment. From aerospace landing gear (via 5160 steel’s fatigue resistance) to renewable energy turbines (via 1045 steel’s cost efficiency), these materials continue to evolve through advanced manufacturing, circular economy practices, and Industry 4.0 integration. For engineers seeking balanced performance and affordability, medium carbon steels provide a robust foundation for next-generation engineering challenges.