Casting aluminum alloys are engineered to produce complex-shaped components via molten metal casting, combining low density, high specific strength, and excellent corrosion resistance. These alloys are categorized into Al-Si, Al-Cu, Al-Mg, and Al-Zn-based systems, each optimized for mechanical performance, thermal stability, or cost efficiency. This report focuses on Al-Si alloy ADC12, Al-Cu alloy ZL201, Al-Mg alloy ZL301, and Al-Zn alloy ADC14, comparing their chemical compositions, physical/mechanical properties, advantages, and industrial applications.
At Huada-Metals Company, we engineer the industry’s most advanced casting aluminum alloys – materials that redefine the boundaries of strength, durability, and manufacturing efficiency. Our alloys represent the pinnacle of metallurgical innovation, offering unmatched performance where conventional metals fail. Welcome to inquire our products and the quality has the asuurance in China. Of course, our price is suitable and afforrable
Overview of Casting Aluminum Alloys
Chemical Composition of Casting Aluminum Alloys
Alloy Grade | Base Metal (%) | Key Alloying Elements (%) | Impurity Limits (%) |
---|---|---|---|
ADC12 (Al-Si-Cu) | Al (Balance) | Si: 9.6–12.0, Cu: 1.5–3.5, Mg: 0.1–0.3, Fe: ≤1.3 | Zn: ≤0.35, Mn: ≤0.5, Sn: ≤0.1 |
ZL201 (Al-Cu) | Al (Balance) | Cu: 4.5–5.3, Mn: 0.6–1.0, Ti: 0.15–0.25 | Fe: ≤0.5, Si: ≤0.5, Mg: ≤0.1 |
ZL301 (Al-Mg) | Al (Balance) | Mg: 9.5–11.0, Mn: 0.1–0.4, Zr: 0.05–0.2 | Fe: ≤0.5, Si: ≤0.3, Cu: ≤0.1 |
ADC14 (Al-Si-Mg-Cu) | Al (Balance) | Si: 10.5–13.0, Mg: 0.1–0.45, Cu: 0.5–2.5, Fe: ≤1.3 | Zn: ≤0.25, Mn: ≤0.5, Ni: ≤0.5 |
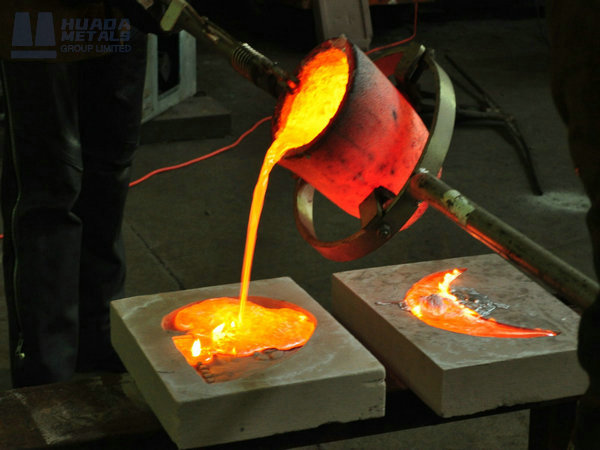
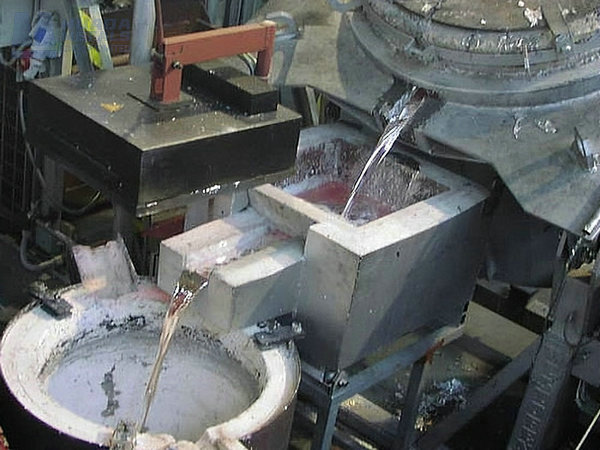
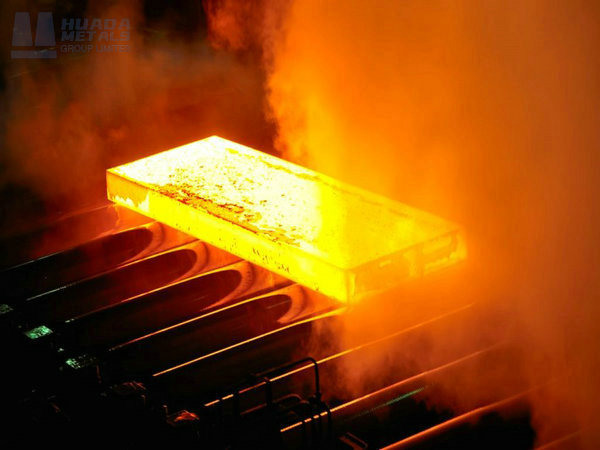
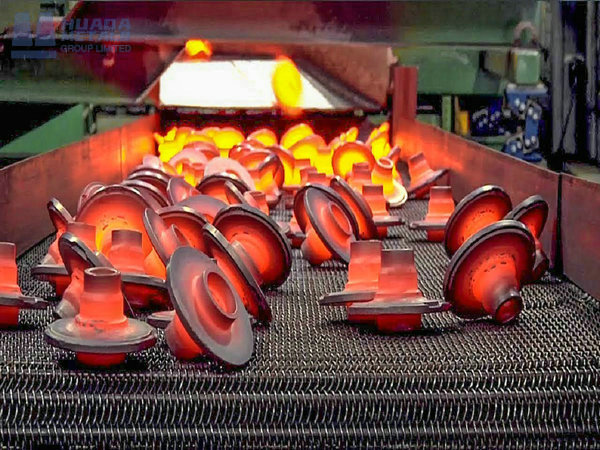
Key Observations:
- ADC12 maximizes Si-Cu content for high fluidity and wear resistance.
- ZL201 incorporates Cu-Mn-Ti alloying for elevated-temperature strength (350–400°C).
- ZL301 exploits high Mg content for corrosion resistance (salt spray >500 h).
- ADC14 balances Si-Mg-Cu for optimized strength-ductility trade-off (UTS ≥280 MPa, EL ≥2%)
Physical & Mechanical Properties
Property | ADC12 | ZL201 | ZL301 | ADC14 |
---|---|---|---|---|
Density (g/cm³) | 2.68 | 2.78 | 2.65 | 2.70 |
Melting Point (°C) | 575–595 | 548–582 | 638–652 | 580–600 |
Tensile Strength (MPa) | 280–320 | 330–380 | 280–310 | 290–330 |
Elongation (%) | 1.5–3.0 | 4–6 | 9–12 | 2.0–3.5 |
Thermal Expansion (×10⁻⁶/°C, 20–100°C) | 21.5 | 23.2 | 24.5 | 22.0 |
Thermal Conductivity (W/m·K) | 96–105 | 120–135 | 150–165 | 100–110 |
Brinell Hardness (HB) | 75–95 | 90–110 | 65–80 | 80–95 |
Key Observations:
- ADC12 exhibits moderate strength (UTS 300 MPa) with high wear resistance (HRC 50–55).
- ZL201 achieves superior high-temperature strength (UTS 350 MPa at 300°C).
- ZL301 offers ultra-low density (2.65 g/cm³) and excellent seawater corrosion resistance.
- ADC14 balances strength (UTS 310 MPa) and toughness (EL 2.5%) via T6 heat treatment.
Key Advantages of Casting Aluminum Alloys
Feature | ADC12 | ZL201 | ZL301 | ADC14 |
---|---|---|---|---|
Castability | Excellent (thin walls: 1.5 mm) | Moderate (porosity risk) | Good (no hot tearing) | Very good (2.0 mm walls) |
Machinability | Moderate (tool wear) | High (chip breaking) | Excellent (burr-free) | Good (HSS tools) |
Corrosion Resistance | Poor (anodizing required) | Moderate (Cu-induced pitting) | Excellent (5% NaCl >1000 h) | Fair (corrosion rate 0.1 mm/y) |
Weldability | Poor (cracking) | Very poor (heat-affected zone softening) | Fair (TIG welding) | Moderate (filler metal required) |
Cost-Performance Ratio | High (automotive) | Moderate (aerospace) | Low (marine) | High (high-volume) |
Manufacturing Processes & Cost Considerations
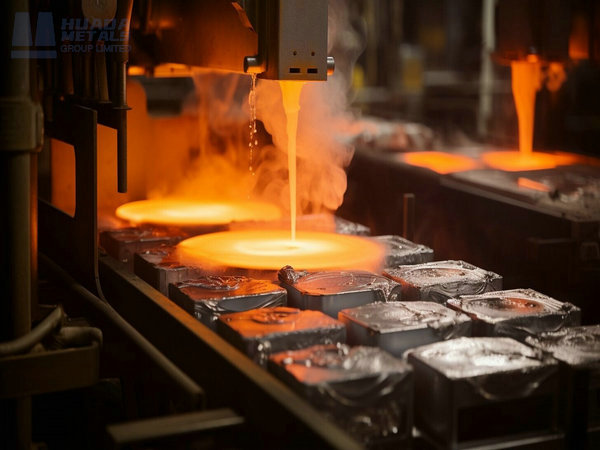
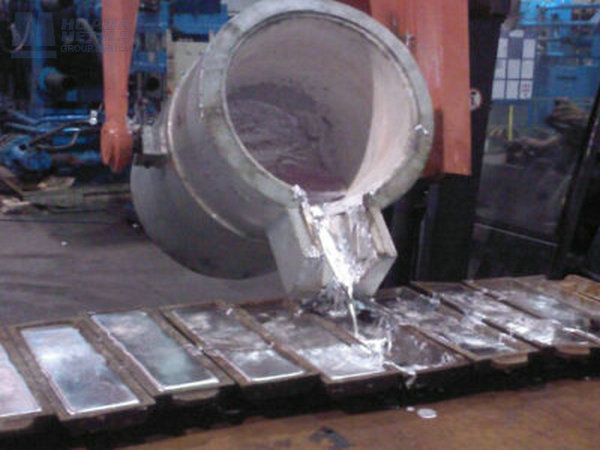
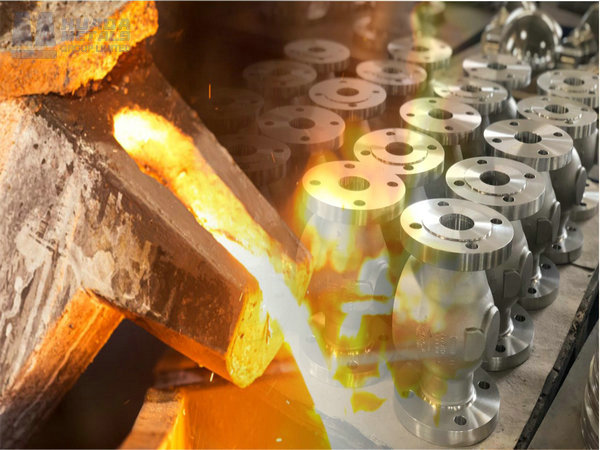
Industry Applications of Casting Aluminum Alloys
Industry | ADC12 | ZL201 | ZL301 | ADC14 |
---|---|---|---|---|
Automotive | Engine blocks, pistons | Turbocharger housings | Oil pans, heat exchangers | Battery enclosures |
Aerospace | Instrument brackets | Wing spars, turbine blades | Landing gear components | Actuator housings |
Marine | Propellers, rudders | Submarine periscopes | Hull structures | Deck fittings |
Electronics | CPU heat sinks | High-voltage connectors | 5G base station covers | Power electronics casings |
Construction | Architectural facades | Seismic dampers | Bridge deck panels | Lighting fixtures |
Quality Standards & Certifications
Cost Considerations
- ADC12: $2.2–2.5/kg (low-cost, high-volume production).
- ZL201: $5.0–6.5/kg (premium aerospace grade).
- ZL301: $3.0–4.0/kg (marine-grade corrosion resistance).
- ADC14: $2.8–3.2/kg (EV-optimized composition).
High-Performance Use Cases:
- ZL201 in hypersonic vehicle leading edges withstands 1,200°C reentry heat fluxes.
- ZL301 in offshore wind turbine nacelles reduces maintenance costs by 60%.
In Conclusion
Casting aluminum alloys remain irreplaceable in industries demanding lightweight, corrosion-resistant, and thermally stable components. While ADC12 dominates mass-produced automotive parts, ZL201 excels in extreme-temperature aerospace applications, ZL301 in marine corrosion resistance, and ADC14 in electric vehicle lightweighting.
Future Trends:
- Additive manufacturing of ZL201 reduces machining waste by 70% in complex turbine blades.
- Graphene-reinforced ADC14 achieves UTS >400 MPa for next-gen EV motors.
- ZL301 with Sc-Zr microalloying extends service life to 50 years in seawater.
Welcome to inquiry and ask for the lastest price, please contact us.