HuaDa Metals has the alloy products and the quality is good, our company has the customerized service for every clients. This article provides a data-driven comparison of five critical high-performance alloys: Hastelloy, Incoloy, Inconel, Monel, and Titanium alloys. Each alloy offers unique properties for extreme environments in aerospace, chemical processing, marine, and energy industries.
Overview of Alloy
Enhanced Strength: Alloys often exhibit greater strength than pure metals.
Corrosion Resistance: Certain alloys resist rust and chemical degradation.
Thermal & Electrical Conductivity: Some alloys optimize conductivity for specific applications.
Lightweight: Many alloys (e.g., aluminum alloys) offer high strength-to-weight ratios.
Customizability: Alloy compositions can be tailored for hardness, ductility, or other properties.
Chemical Composition of Alloy
Element | Hastelloy C276 | Incoloy 825 | Inconel 718 | Monel 400 | Ti-6Al-4V |
---|---|---|---|---|---|
Ni | Bal. (52-62%) | 38-46% | 50-55% | 63-70% | – |
Cr | 14.5-16.5% | 19.5-23.5% | 17-21% | – | – |
Mo | 15-17% | 2.5-3.5% | 2.8-3.3% | – | – |
Fe | 4-7% | Bal. | Bal. | ≤2.5% | ≤0.25% |
Al | – | – | 0.2-0.8% | – | 5.5-6.5% |
Ti | – | 0.6-1.2% | 0.65-1.15% | – | Bal. (90%) |
Cu | – | 1.5-3.0% | – | 28-34% | – |
Co | ≤2.5% | – | – | – | – |
Physical Properties of Alloy
Property | Hastelloy C276 | Incoloy 825 | Inconel 718 | Monel 400 | Ti-6Al-4V |
---|---|---|---|---|---|
Density (g/cm³) | 8.89 | 8.14 | 8.19 | 8.80 | 4.43 |
Melting Range (°C) | 1323-1371 | 1370-1400 | 1260-1336 | 1300-1350 | 1604-1660 |
Thermal Conductivity (W/m·K) | 10.2 | 11.1 | 11.4 | 21.8 | 6.7 |
CTE (10⁻⁶/°C, 20-100°C) | 11.2 | 14.0 | 13.0 | 13.9 | 8.6 |
Electrical Resistivity (μΩ·m) | 1.30 | 1.15 | 1.25 | 0.54 | 1.78 |
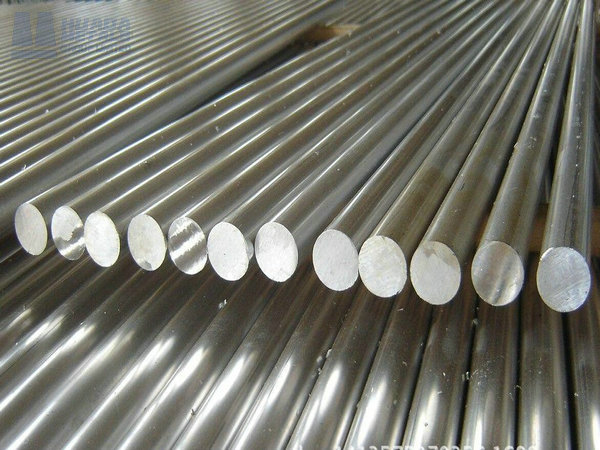
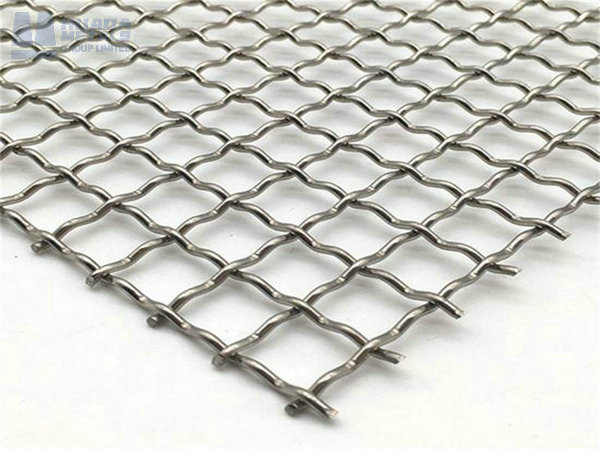
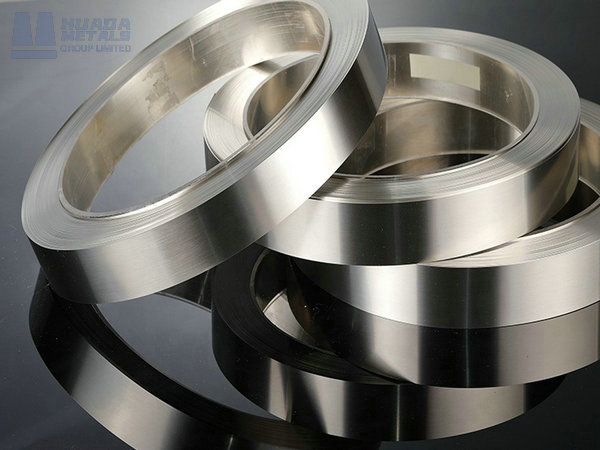
Mechanical Properties of Alloy
Property | Hastelloy C276 | Incoloy 825 | Inconel 718 | Monel 400 | Ti-6Al-4V |
---|---|---|---|---|---|
Tensile (MPa) | 690 | 586 | 1275 | 480 | 930 |
Yield (MPa) | 283 | 241 | 1034 | 170 | 869 |
Elongation (%) | 40 | 30 | 12 | 35 | 10 |
Hardness (HV) | 200 | 180 | 350 | 150 | 330 |
Fatigue Limit (MPa) | 280 | 240 | 550 | 180 | 500 |
Advantages and Benifits of Alloy
✔ Higher Strength & Durability – Alloys often outperform pure metals in load-bearing applications.
✔ Better Corrosion Resistance – Stainless steel, titanium alloys, and nickel alloys resist oxidation.
✔ Tailored Properties – Engineers can adjust alloy compositions for specific needs (e.g., lightweight, heat resistance).
✔ Cost-Effectiveness – Some alloys reduce material costs while maintaining performance.
Alloy | Top 3 Advantages | Main Limitations |
---|---|---|
Hastelloy C276 | 1. Best HCl resistance 2. Excellent pitting resistance 3. Good weldability | High cost ($45-65/kg) |
Incoloy 825 | 1. Sulfuric acid resistance 2. Cost-effective 3. Good fabricability | Limited to 400°C |
Inconel 718 | 1. 700°C strength 2. Oxidation resistant 3. Age-hardenable | Difficult machining |
Monel 400 | 1. Seawater corrosion-proof 2. Non-magnetic 3. Easy to form | Poor high-temp performance |
Ti-6Al-4V | 1. Highest strength/weight 2. Biocompatible 3. Fatigue resistant | Expensive ($80-120/kg) |
Industrial Applications of Alloys
Aerospace: Titanium & aluminum alloys for airframes and engines.
Automotive: Steel alloys for chassis; aluminum alloys for lightweighting.
Construction: Steel-reinforced concrete, aluminum cladding.
Electronics: Copper alloys in circuits; magnesium alloys in laptops.
Medical: Titanium & cobalt-chromium alloys for implants.
Energy: Nickel superalloys in gas turbines; aluminum in solar panels.
Industry | Hastelloy | Incoloy | Inconel | Monel | Titanium |
---|---|---|---|---|---|
Oil & Gas | Downhole tools | Pipe systems | Turbine blades | Marine hardware | Subsea components |
Aerospace | – | – | Jet engines | – | Airframe structures |
Chemical | Reactor vessels | Heat exchangers | Valves | Pump shafts | Heat exchangers |
Medical | – | – | – | – | Implants |
Nuclear | Waste containers | – | Reactor parts | – | Coolant pipes |
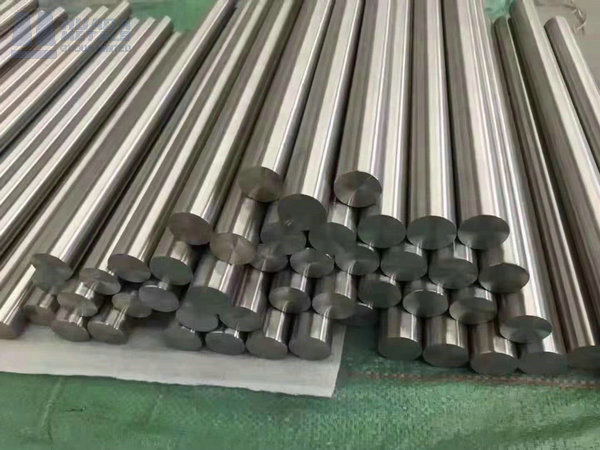
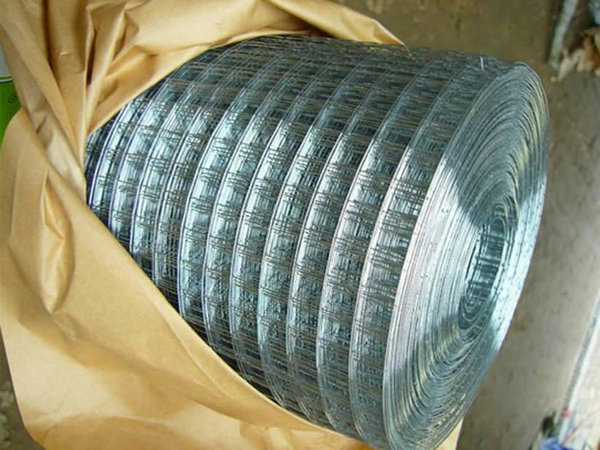
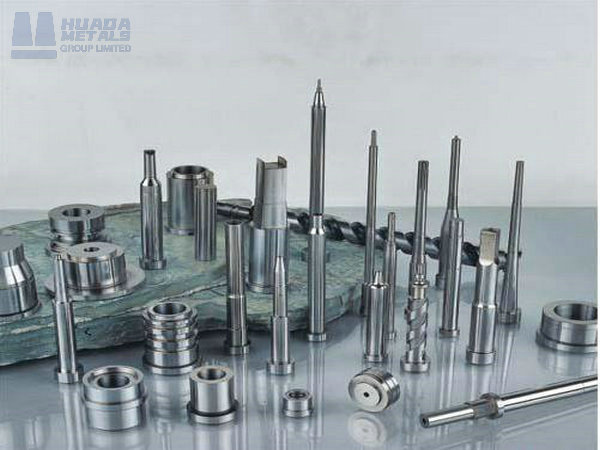
Cost Analysis (2025 Market)
Alloy | Price (USD/kg) | Lifespan (Years) | Cost per Year* |
---|---|---|---|
Hastelloy C276 | $50-70 | 20-25 | $2.80 |
Incoloy 825 | $25-35 | 15-20 | $1.75 |
Inconel 718 | $60-80 | 25-30 | $2.67 |
Monel 400 | $30-40 | 20+ | $1.80 |
Ti-6Al-4V | $90-120 | 30+ | $3.50 |
*Assuming 20-year lifespan for calculation
Cost-Effectiveness Insight:
Incoloy 825 offers the best balance of performance & cost
Titanium has the highest upfront cost but longest service life
In Conclusion
Final Recommendations:
For acid environments → Choose Hastelloy C276
Budget-conscious projects → Incoloy 825
Aerospace/650°C+ → Inconel 718
Marine/seawater → Monel 400
Weight-critical designs → Ti-6Al-4V
Key Takeaway:
Each alloy serves distinct extreme conditions. Selection should consider:
✔ Chemical exposure
✔ Mechanical load requirements
✔ Temperature range
✔ Total lifecycle cost
Alloys are fundamental to modern engineering, offering superior performance compared to pure metals. From everyday items like coins and smartphones to critical aerospace and medical applications, alloys drive innovation across industries. Alloys are engineered materials made by combining two or more metallic elements (or a metal with non-metallic elements) to enhance specific properties such as strength, corrosion resistance, conductivity, or durability. They are widely used across industries, including aerospace, automotive, construction, electronics, and medical technology.