Pure aluminum alloys (1xxx series) consist of 99.0% to 99.99% aluminum with minimal alloying elements, offering unmatched electrical conductivity, corrosion resistance, and formability. These alloys are essential for applications requiring high reflectivity, thermal management, or chemical purity.
Grade | Al% | Fe% | Si% | Cu% | Other | Conductivity (%IACS) |
---|---|---|---|---|---|---|
1050 | 99.50 | 0.40 | 0.25 | 0.05 | Zn 0.05 | 61 |
1060 | 99.60 | 0.35 | 0.20 | 0.03 | Ti 0.03 | 62 |
1100 | 99.00 | 0.95 | 0.95 | 0.05-0.20 | – | 59 |
1199 | 99.99 | 0.006 | 0.006 | 0.006 | – | 64 |
Pure aluminum alloys, primarily composed of aluminum (99.0%+ purity) with minimal additions of elements like copper, magnesium, manganese, or silicon, are engineered to balance lightweight properties with enhanced mechanical and corrosion-resistant characteristics. These alloys are foundational in industries prioritizing durability, energy efficiency, and sustainability.
AA 1050/1060 (99.5%+ Aluminum)
- Key Features:
- Ultra-high purity for electrical conductivity and chemical resistance.
- Applications:
- Electrical conductors, reflective surfaces, chemical processing equipment, and decorative panels.
AA 3003 (Manganese-Enhanced)
- Key Features:
- 1.0–1.5% manganese improves strength (UTS ~145 MPa) while retaining formability.
- Applications:
- Cookware, HVAC ducting, roofing, and automotive heat shields.
AA 5052 (Magnesium-Alloyed)
- Key Features:
- 2.2–2.8% magnesium enhances corrosion resistance (especially in marine environments) and fatigue strength.
- Applications:
- Marine structures, fuel tanks, pressure vessels, and architectural cladding.
AA 6061 (Heat-Treatable Alloy)
- Key Features:
- 0.6% silicon and 1.0% magnesium enable precipitation hardening (UTS ~290 MPa post-T6 treatment).
- Applications:
- Aerospace components, bicycle frames, automotive parts, and yacht fittings.
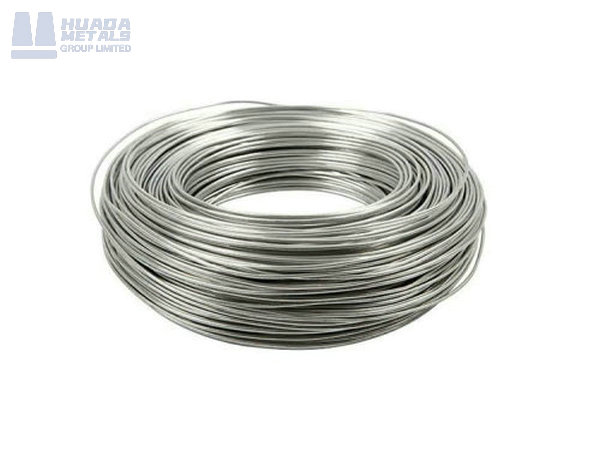
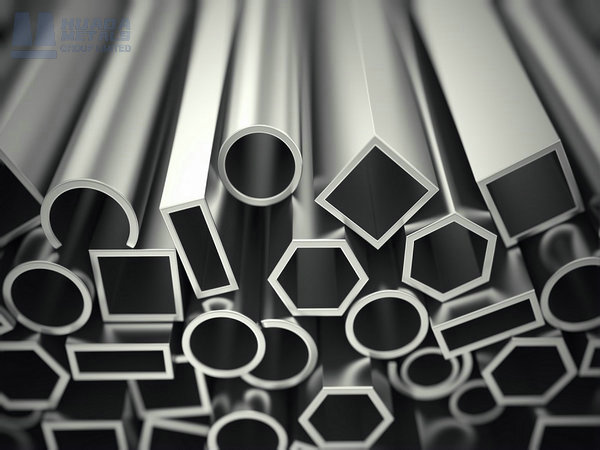
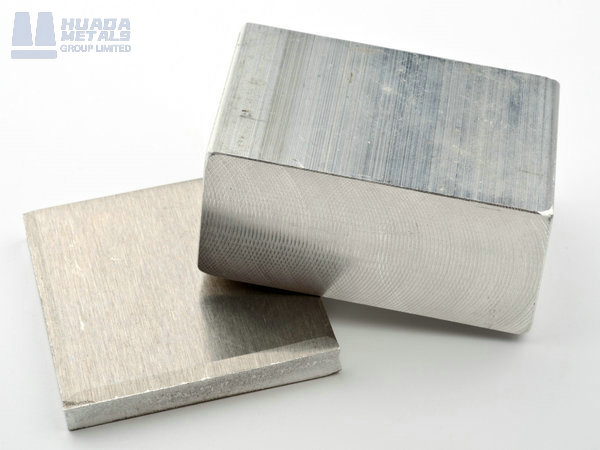
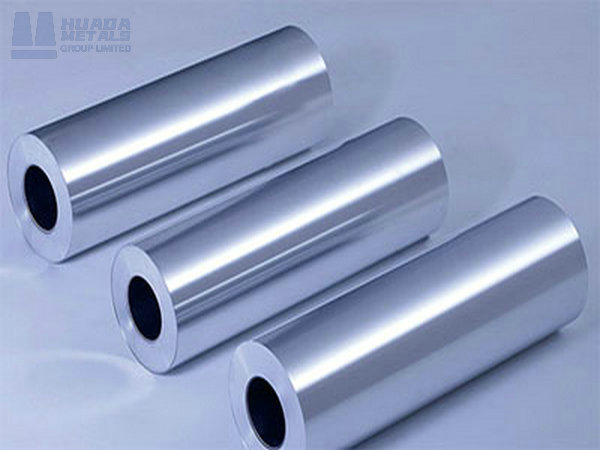
Key Properties and Advantages of Pure Aluminum
- Lightweight Strength:
Pure aluminum alloys offer a density of ~2.7 g/cm³ (one-third that of steel) while maintaining adequate strength, making them ideal for weight-sensitive applications. - Corrosion Resistance:
A self-forming, adherent aluminum oxide (Al₂O₃) layer provides inherent protection against atmospheric, marine, and industrial corrosion, extending component lifespan. - Thermal and Electrical Conductivity:
Excellent heat dissipation (237 W/m·K) and electrical conductivity (62% IACS) suit applications in heat exchangers, power transmission, and electronics. - Formability and Machinability:
High ductility enables deep drawing, extrusion, and stamping, while good machinability reduces production costs. - Sustainability:
100% recyclable without degradation, aligning with circular economy goals.
Distinctive Properties
✔ Corrosion Resistance
Forms a self-healing oxide layer for protection in marine/chemical environments
Resistant to nitric acid, organic acids, and oxidizing salts
✔ Electrical & Thermal Conductivity
61-64% IACS conductivity (vs. copper at 100%)
Thermal conductivity: 120-230 W/m·K (alloy-dependent)
✔ Formability & Weldability
Excellent cold-working capability (up to 80% reduction)
All-position weldable (TIG, MIG, laser)
✔ Reflectivity & Aesthetics
88-92% visible light reflectivity (polished surface)
Non-sparking for explosive environments
Applications Industry of Pure Aluminum
1. Electrical & Electronics
Busbars and power transmission lines
Capacitor foils (ultra-pure 1199)
Semiconductor heat sinks
2. Chemical Processing
Nitric acid storage tanks
Pharmaceutical packaging (foil for blister packs)
- Reflective roofing for energy efficiency
3. Architecture & Decoration
Decorative trim with anodized finishes
4. Food & Packaging
Beverage can bodies (1100 alloy)
Flexible packaging foil (6-20µm thickness)
5. Specialized Industrial
Cryogenic components (low-temperature ductility)
PVD coating substrates for optics
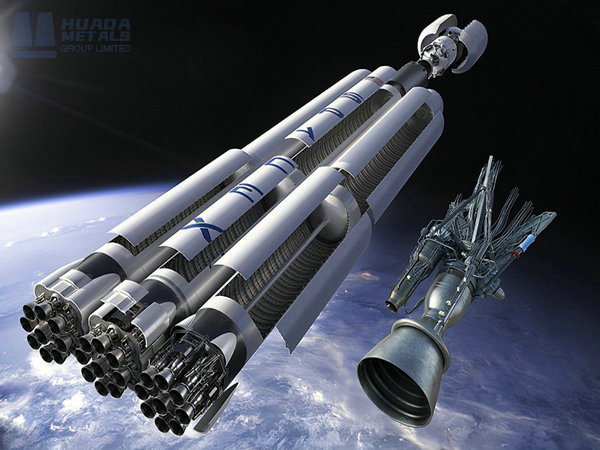
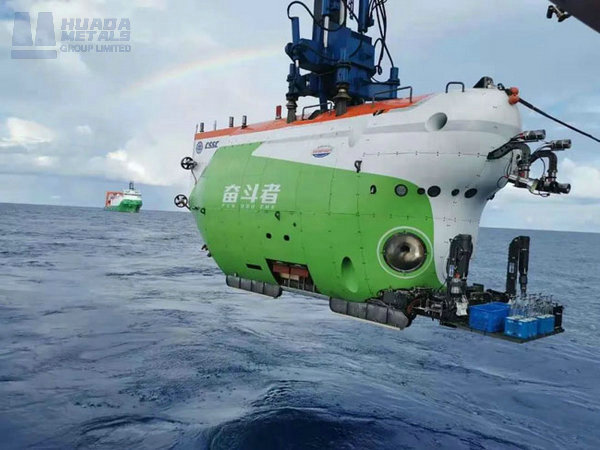
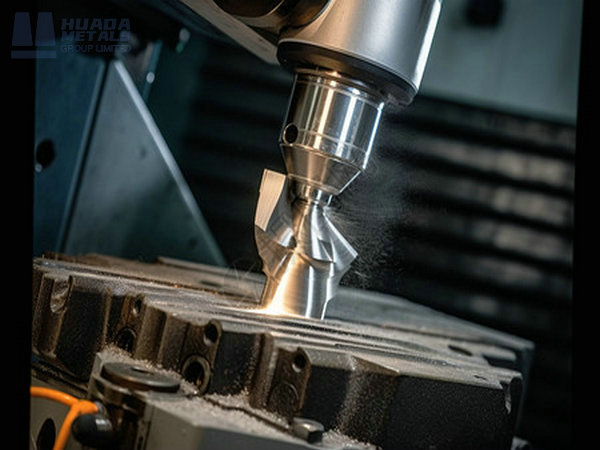
Sector | Application Examples |
---|---|
Aerospace | Fuselage skins, hydraulic tubing, cryogenic fuel tanks (SpaceX Starship). |
Electronics | Printed circuit board traces, RF shields, and 5G base station heat spreaders. |
Automotive | Electric vehicle battery casings (Tesla Model 3) and lightweight engine blocks. |
Construction | Unitized curtain walls (Burj Khalifa) and fire-resistant roofing. |
Packaging | Ultrathin foil (6 μm) for pharmaceutical blisters and aseptic food containers. |
Manufacturing and Processing of Pure Aluminum
- Melting and Casting:
Produced via direct-chill (DC) casting or continuous casting to refine grain structure and reduce impurities. - Forming:
- Hot forming at 350–500°C for complex shapes.
- Cold forming (e.g., deep drawing) for precision parts.
- Heat Treatment:
- Solution annealing (530°C) and artificial aging (175°C, 8h) for 6xxx series alloys.
- Surface Finishing:
- Anodizing (hard-coat or decorative) for wear and corrosion resistance.
- Powder coating for aesthetic and protective layers.
- Lightweight Strength: Enables fuel-efficient aircraft structures (e.g., Airbus A380 wing skins).
- Electromagnetic Shielding: Non-magnetic properties make it indispensable in MRI machines and satellite electronics.
- Recyclability: 95% energy savings vs. primary production, aligning with circular economy goals.
- Aesthetic Versatility: Anodized coatings provide corrosion resistance and vibrant colors for architectural facades.
Available Product Forms
Foils (0.006mm – 0.2mm)
Sheets/Plates (0.2mm – 150mm)
Rods/Wire (1mm – 300mm diameter)
Extrusions (Custom profiles)
Quality Standards
ASTM B209/B479 for sheet/foil
EN 573-1 for chemical composition
RoHS/REACH compliant for electronics
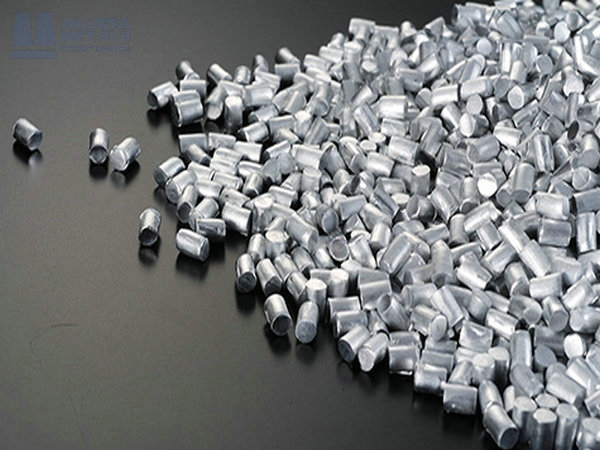
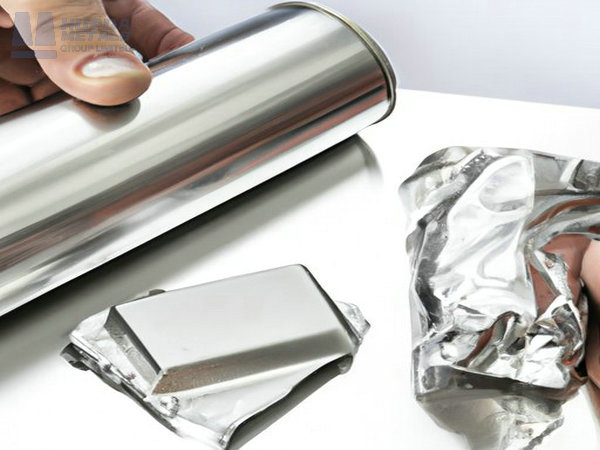
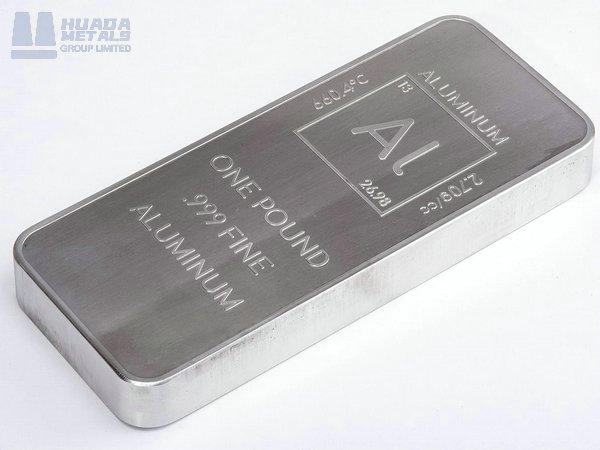
Environmental and Economic Benefits
- Energy Efficiency:
Reduced weight lowers fuel consumption in transportation and energy use in buildings. - Lifecycle Cost Savings:
Corrosion resistance minimizes maintenance and replacement expenses. - Recyclability:
Scrap aluminum retains ~95% of its original energy input, cutting production emissions by 95% compared to primary aluminum.
Comparison with Other Aluminum Series
Parameter | 1xxx (Pure Al) | 3xxx (Mn Alloy) | 5xxx (Mg Alloy) | 6xxx (Mg-Si) |
---|---|---|---|---|
Strength (MPa) | 50-100 | 100-200 | 150-300 | 200-350 |
Corrosion Resistance | ★★★★★ | ★★★★ | ★★★★★ | ★★★ |
Formability | ★★★★★ | ★★★★ | ★★★ | ★★★★ |
Typical Use | Foils/Conductors | Beverage cans | Marine structures | Automotive frames |
In Conclusion
Pure aluminum’s unique combination of lightweight durability, electrical efficiency, and corrosion immunity positions it as a cornerstone material in modern engineering. Advances in refining and processing continue to expand its applicability, from deep-space probes to next-generation renewable energy systems. For manufacturers seeking sustainable, high-performance solutions, pure aluminum remains an unparalleled choice.
Pure aluminum alloys represent a versatile material solution for industries demanding lightweight, corrosion-resistant, and sustainable engineering. Their adaptability across forming, joining, and finishing processes, coupled with exceptional recyclability, ensures their dominance in modern manufacturing. Whether for aerospace innovation, green building initiatives, or renewable energy systems, pure aluminum alloys continue to redefine performance standards. For technical specifications, alloy selection guidance, or custom fabrication support, contact HuaDa Metals your trusted partner in advanced aluminum solutions. Welcome to inquiry and ask for the lastest price. Contact Us.