Aluminum (Al) is a lightweight, silvery-white metal with atomic number 13. It is the most abundant metal in Earth’s crust (8% by weight) and is widely used in industries due to its:
✔ Low density (2.7 g/cm³) – About 1/3 the weight of steel.
✔ Excellent corrosion resistance – Forms a protective oxide layer.
✔ High electrical & thermal conductivity – Used in power lines and heat exchangers.
✔ Recyclability – Can be reused indefinitely without quality loss.
Aluminum, a silvery-white metal with the atomic number 13, is one of Earth’s most abundant and versatile elements. Often overlooked in favor of flashier materials like steel or titanium, aluminum quietly powers the modern world—from the smartphones in our pockets to the spacecraft exploring distant planets. Let’s dive into why this lightweight metal aluminum foil deserves a spotlight in engineering, sustainability, and everyday innovation.
Types of Aluminum & Common Alloys
Minimum 99.0% aluminum content
Example grades:
1050 (99.5% Al)
1100 (99.0% Al)
Properties:
Excellent corrosion resistance
High electrical/thermal conductivity
Low mechanical strength
Aluminum is rarely used in pure form—alloying enhances strength and workability:
Series | Main Alloying Element | Key Grades | Applications |
---|---|---|---|
1xxx | ≥99% Pure Al | 1050, 1100 | Foil, chemical tanks |
2xxx | Copper (Cu) | 2024, 2014 | Aircraft structures |
3xxx | Manganese (Mn) | 3003, 3004 | Beverage cans, roofing |
5xxx | Magnesium (Mg) | 5052, 5083 | Marine, automotive |
6xxx | Mg + Silicon (Si) | 6061, 6063 | Extrusions, architecture |
7xxx | Zinc (Zn) | 7075, 7050 | Aerospace, defense |
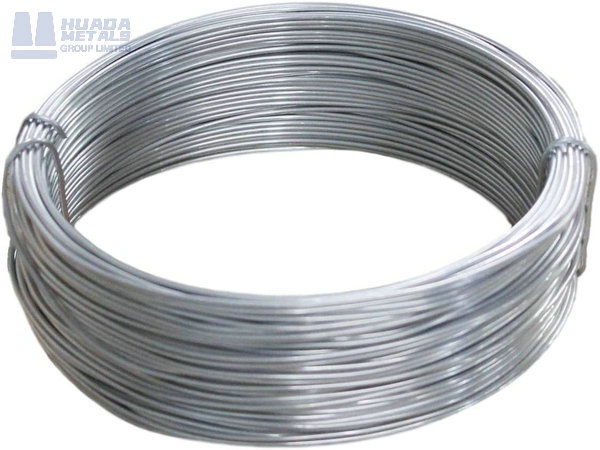
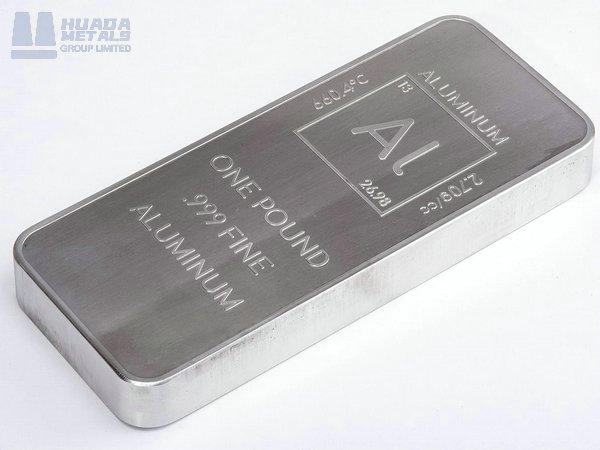
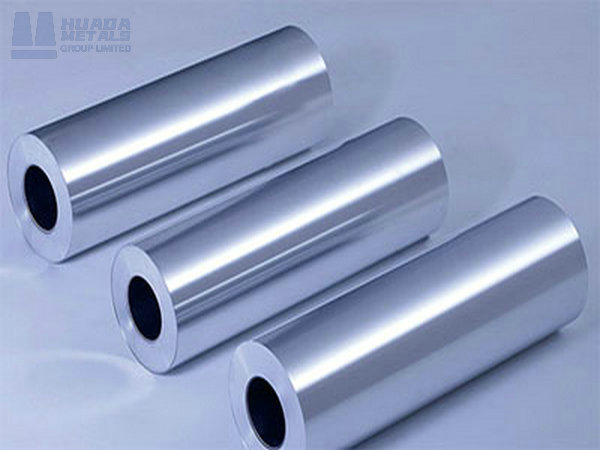
Specification and Size of Aluminum
Aluminum (Al) is a silvery-white, ductile metallic element belonging to Group 13 of the periodic table with:
Atomic number: 13
Atomic weight: 26.9815
Crystal structure: Face-centered cubic (FCC)
Natural occurrence: Always found combined in minerals (primarily bauxite)
Chemical Composition of Aluminum
Alloy Series | Alloy Designation | Chemical Composition (Approximate, wt%) | Key Properties | Typical Applications |
---|---|---|---|---|
1xxx Series | 1050 | Al: ≥99.50 Fe: ≤0.40 Si: ≤0.25 Cu: ≤0.05 | High purity, excellent corrosion resistance, low strength, high electrical conductivity | Chemical processing, electrical conductors, food packaging |
2xxx Series | 2024 | Al: 93.5 Cu: 4.4 Mg: 1.5 Mn: 0.6 | High strength, good fatigue resistance, moderate corrosion resistance | Aircraft structures, automotive parts, rivets |
3xxx Series | 3003 | Al: 98.6 Mn: 1.0–1.5 Fe: ≤0.7 Si: ≤0.6 | Moderate strength, excellent workability, good corrosion resistance | Cooking utensils, building panels, chemical equipment |
4xxx Series | 4043 | Al: 94.7–97.0 Si: 4.5–6.0 Fe: ≤0.8 Cu: ≤0.3 | Low melting point, excellent fluidity, good corrosion resistance | Welding wire, brazing alloys, filler materials |
5xxx Series | 5083 | Al: 94.8–97.7 Mg: 4.0–4.9 Mn: 0.40–1.0 Cr: 0.05–0.25 | High strength, excellent corrosion resistance (especially marine), good weldability | Marine structures, pressure vessels, automotive parts |
6xxx Series | 6061 | Al: 95.8–98.6 Mg: 0.8–1.2 Si: 0.4–0.8 Cu: ≤0.40 Cr: ≤0.25 | Good strength, excellent formability, good corrosion resistance, heat-treatable | Aerospace components, automotive parts, bicycle frames |
7xxx Series | 7075 | Al: 87.1–91.4 Zn: 5.1–6.1 Mg: 2.1–2.9 Cu: 1.2–2.0 Cr: 0.18–0.28 | Very high strength, good fatigue resistance, moderate corrosion resistance | Aircraft structures, high-stress components, sporting goods |
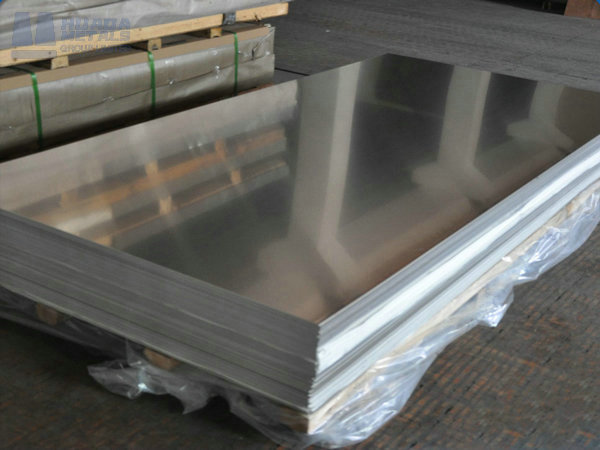
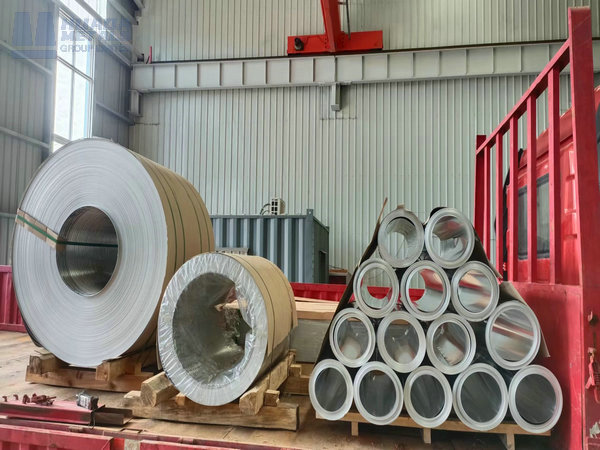
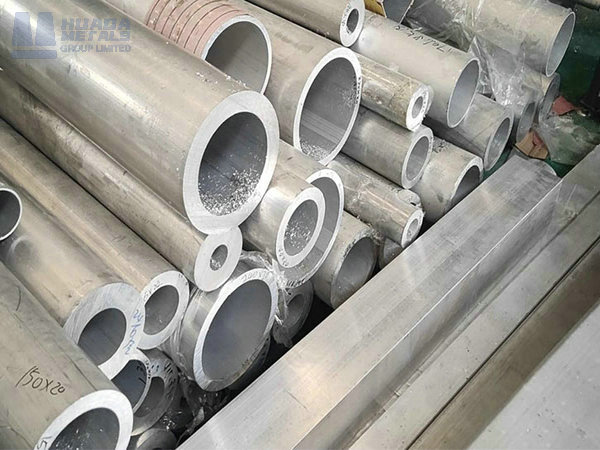
Core Physical Properties of Aluminum
Property | Value | Significance |
---|---|---|
Density | 2.70 g/cm³ | 1/3 the weight of steel |
Melting point | 660.3°C | Lower than most structural metals |
Electrical conductivity | 37.7 MS/m (61% IACS) | 2x better than steel |
Thermal conductivity | 237 W/(m·K) | Excellent heat dissipation |
CTE (20-100°C) | 23.1 μm/m·°C | Requires joint design consideration |
Aluminum is the second-most used metal globally after steel, valued for its lightweight, corrosion resistance, and excellent formability. Its applications span virtually every industrial sector, from transportation to construction and electronics. From a sustainability perspective, aluminum’s infinite recyclability with only 5% of the energy required for primary production makes it a cornerstone of circular economy initiatives across all these industries. Ongoing alloy development continues to expand aluminum’s capabilities, ensuring its position as a critical material for both current industrial needs and future technological advancements.
Industrial Applications of Aluminum
Aluminum has become indispensable across modern industries due to its unique combination of properties including lightweight characteristics, excellent corrosion resistance, and outstanding formability. This versatile metal finds applications in nearly every industrial sector, with its usage patterns and alloy selections varying significantly based on specific technical requirements.
Industry | Key Applications | Preferred Alloys | Why Aluminum? | Competing Materials |
---|---|---|---|---|
Transportation | Aircraft fuselages, car bodies, ship hulls | 2024, 7075, 5083 | 40-60% weight savings vs. steel | Steel, composites |
Construction | Window frames, roofing, bridges | 6061, 6063, 3003 | Corrosion resistance, longevity | Steel, PVC |
Packaging | Beverage cans, foil, containers | 3004, 5182, 8011 | Lightweight, barrier properties | Plastic, glass |
Electrical | Power lines, heat sinks, busbars | 1350, 6101, 6061 | 61% IACS conductivity | Copper |
Consumer Goods | Electronics, appliances, furniture | 5052, 6061, 7075 | Aesthetic finishes, durability | Stainless steel |
Industrial | Heat exchangers, piping, machinery | 3003, 5052, 6061 | Thermal conductivity, weldability | Carbon steel |
In the transportation sector, aluminum plays a critical role in weight reduction strategies. Aerospace applications extensively utilize high-strength alloys like 2024 and 7075 for airframe components, where their superior strength-to-weight ratio provides significant fuel efficiency advantages. The automotive industry has increasingly adopted aluminum for body panels (using 5xxx series alloys) and structural components (6xxx series), achieving 40-60% weight savings compared to traditional steel constructions. Marine applications benefit from the exceptional seawater corrosion resistance of 5xxx series alloys in hull constructions and superstructures.
The construction industry values aluminum for its durability and low maintenance requirements. Alloys such as 6061 and 6063 dominate architectural applications including curtain walls, window frames, and roofing systems, where their natural oxide layer provides long-term protection against atmospheric corrosion. Bridge builders select aluminum for its lightweight properties in movable bridge components, while the metal’s high reflectivity makes it ideal for lighting fixtures and solar reflectors.
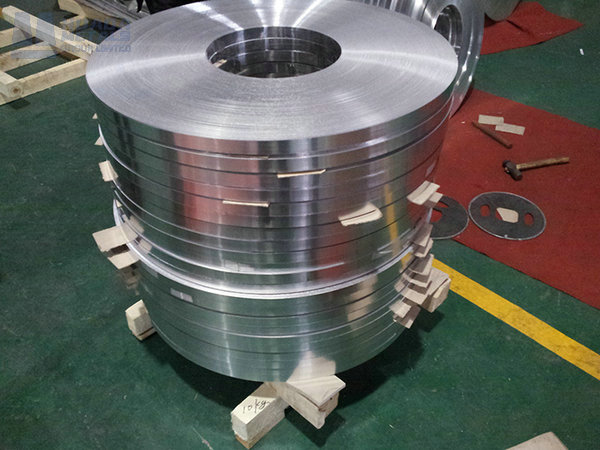
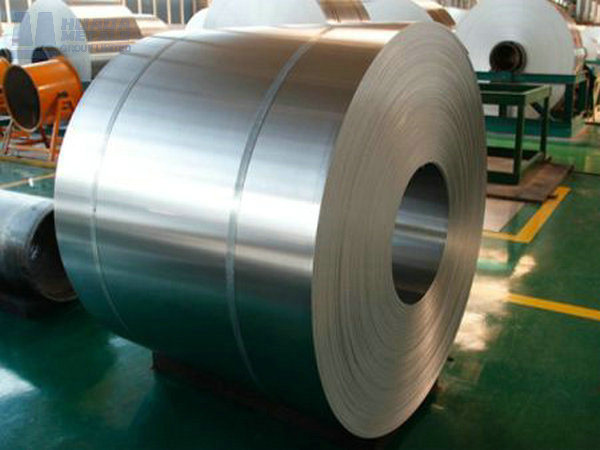
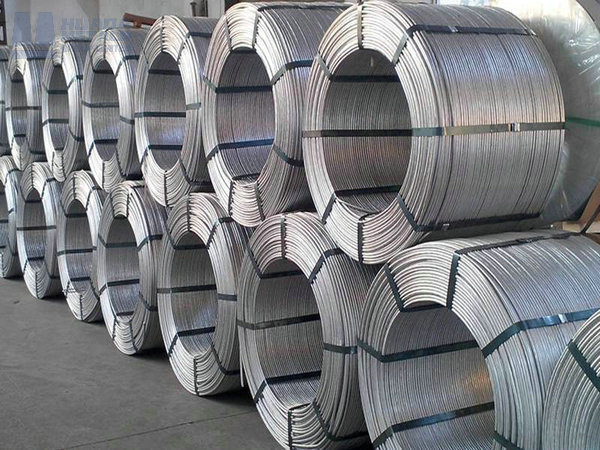
Comparison with Competing Materials
Property | Aluminum | Steel | Titanium |
---|---|---|---|
Density (g/cm³) | 2.7 | 7.85 | 4.5 |
Strength-to-weight | High | Medium | Very High |
Corrosion Resistance | Excellent | Poor | Outstanding |
Cost (USD/kg) | 2.5-5.0 | 0.5-1.5 | 15-30 |
Thermal Conductivity | Very High | Low | Low |
The Future of Aluminum: Innovations on the Horizon
Advanced Manufacturing: From Casting to 3D Printing
- Additive Manufacturing: Aluminum-silicon alloys (e.g., AlSi10Mg) dominate 3D printing for lightweight prototypes and end-use parts.
- Friction Stir Welding (FSW): Joins aluminum without melting, reducing defects in automotive and aerospace assemblies.
Nanotechnology & Composites: Breaking Strength Limits
- Graphene-Aluminum Composites: 500% stronger than pure aluminum (used in SpaceX’s Starship heat shields).
- Ceramic-Reinforced Aluminum: Aluminum oxide (Al₂O₃) nanoparticles boost stiffness for engine components.
Smart Materials: Responsive to Environmental Changes
- Shape-Memory Alloys: Aluminum-zinc alloys return to original shape after deformation (useful for deployable satellites).
- Self-Healing Coatings: Polymer-aluminum composites repair cracks autonomously via microcapsules.
Decarbonization Roadmap: 2030 & Beyond
- Global Targets:
- 30% reduction in CO₂ emissions by 2030 (via green energy and recycling).
- 50% recycled content in aluminum products by 2040.
- Case Study: Norway’s Hydro Circular initiative aims to produce “zero-carbon” aluminum by 2030 using hydropower and scrap.
In Conclusion
Aluminum’s unique combination of light weight, corrosion resistance, and formability makes it indispensable across modern industries. While pure aluminum offers excellent conductivity and corrosion resistance, its alloy systems enable tailored solutions for applications ranging from beverage cans to spacecraft components.
The metal’s recyclability and sustainability position it as a key material for the green economy, though energy-intensive primary production remains an environmental challenge. Ongoing developments in alloy technology and manufacturing processes continue to expand aluminum’s applications in transportation, construction, and energy sectors. Please contact us or inquire the lastest price.