High carbon steels is a ferrous alloy containing 0.6% to 1.5% carbon, offering exceptional hardness, wear resistance, and strength after heat treatment. While less ductile than low-carbon steels, it is indispensable for applications requiring cutting edges, high strength, and durability.
High carbon steel, classified as a carbon tool steel, typically contains carbon in the range of 0.60% to 1.70%, with optional alloy additions like manganese, silicon, or chromium. This steel grade is renowned for its exceptional hardness, wear resistance, and elastic limit, making it indispensable in industries requiring durable, high-performance components.
Overview of High Carbon Steel
Chemical Composition of High Carbon Steel
- Higher carbon content enhances hardness but reduces toughness.
- Alloying elements like Cr improve wear resistance and corrosion resistance.
Grade | C (%) | Mn (%) | Si (%) | Other Elements | Key Features |
---|---|---|---|---|---|
AISI 1060 | 0.55-0.65 | 0.60-0.90 | 0.15-0.35 | – | General-purpose tool steel |
AISI 1095 | 0.90-1.03 | 0.30-0.50 | 0.20-0.30 | – | High hardness, blades & springs |
AISI 52100 | 0.98-1.10 | 0.25-0.45 | 0.15-0.35 | 1.3-1.6% Cr | Bearing steel, wear-resistant |
W1 Tool Steel | 0.95-1.10 | 0.10-0.40 | 0.10-0.30 | – | Water-hardening, cutting tools |

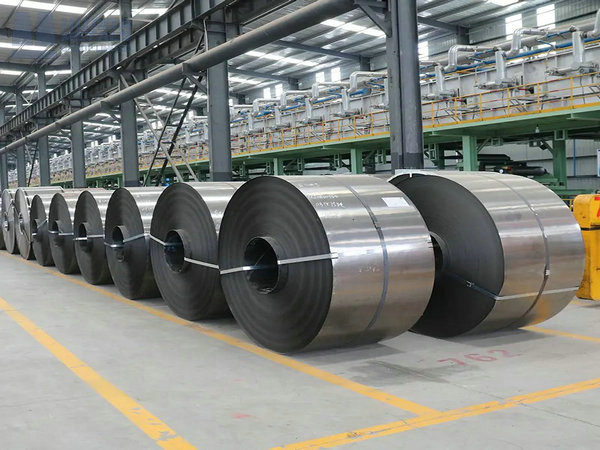
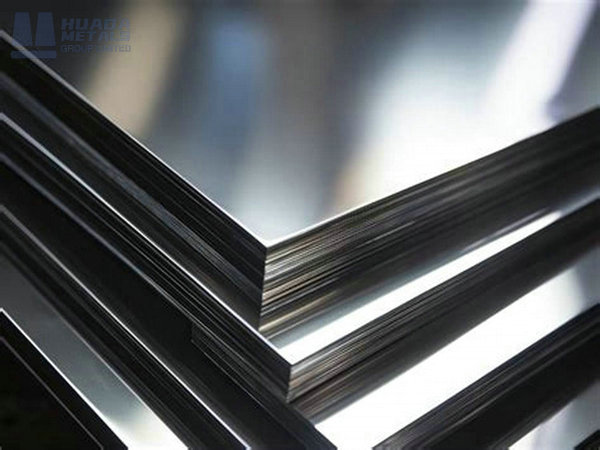
Physical Properties of High Carbon Steel
Property | 1060 | 1095 | 52100 | W1 |
---|---|---|---|---|
Density (g/cm³) | 7.85 | 7.85 | 7.81 | 7.83 |
Melting Point (°C) | 1425-1540 | 1425-1540 | 1425-1540 | 1425-1540 |
Thermal Conductivity (W/m·K) | 49 | 48 | 46 | 47 |
Electrical Resistivity (μΩ·cm) | 15.9 | 16.2 | 16.5 | 16.0 |
Mechanical Properties of High Carbon Steel
Grade | Tensile Strength (MPa) | Yield Strength (MPa) | Elongation (%) | Hardness (HRC) |
---|---|---|---|---|
1060 | 620-800 | 480-620 | 12-15 | 55-62 |
1095 | 850-1100 | 650-900 | 5-10 | 60-65 |
52100 | 950-1200 | 700-900 | 5-8 | 62-66 |
W1 | 900-1150 | 700-950 | 4-8 | 64-67 |
Key Advantages of High Carbon Steel
- High Hardness & Wear Resistance: Ideal for cutting tools, bearings, and springs.
- Cost-Effective: Raw materials are abundant, and production costs are lower than alloy steels.
- Heat Treatability: Allows precise control of hardness and toughness via quenching, tempering, or surface hardening.
- Elastic Limit: Suitable for springs and components requiring high resilience.
Limitations:
- Poor Weldability: High carbon content leads to cracking; requires preheating/post-weld treatments.
- Low Toughness at High Temps: Hardness drops above 200°C, limiting use in high-heat applications
HuaDa Metals has the various shape of the carbon steel content: 0.25%-0.60% Properties: Increased strength and hardness, decreased ductility and toughness, preheating for welding. Applications: Gears, shaft parts, machine tool guides. Examples: 45 steel (carbon content 0.42%-0.50).
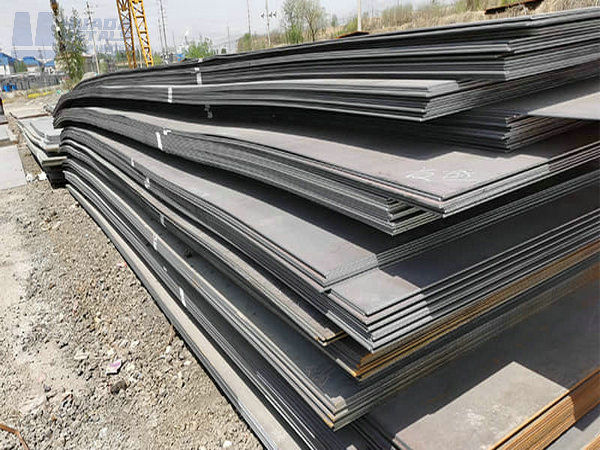
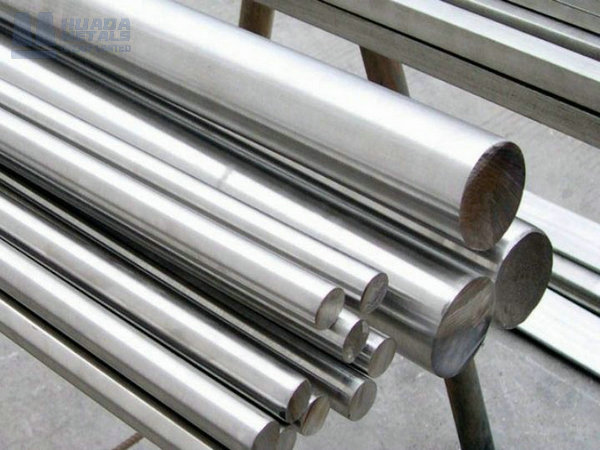
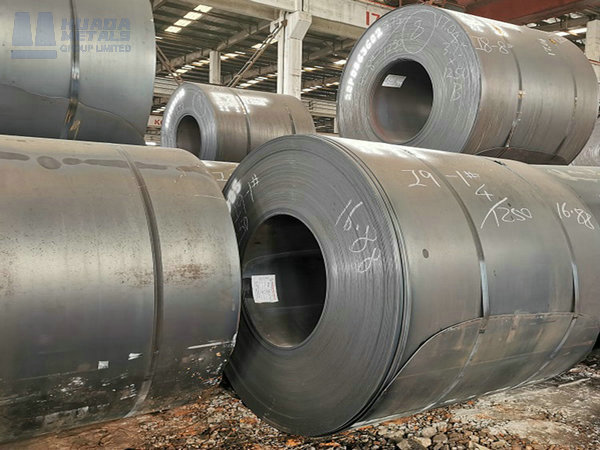
Manufacturing Processes of High Carbon Steel
Primary Production Routes
- Electric Arc Furnace (EAF) Recycling:
- Dominates medium carbon steel production (70% market share) due to lower capital costs (150/tonvs.250/ton for BOF).
- Cost: 0.8–1.0/kg (includes scrap, energy, and alloys).
- Basic Oxygen Furnace (BOF) Steelmaking:
- Preferred for high-volume production (e.g., 1 million tons/year at Nippon Steel’s Kimitsu plant).
- Cost: 0.7–0.9/kg (with iron ore and coke inputs).
- Hot Forging:
- 1045 steel billets forged at 1,100–1,200°C into crankshafts (die life: 5,000–8,000 cycles with TiN coating).
- Cost Drivers: Die wear (10,000–20,000 per set) and energy (1.2 kWh/kg forging energy).
- Cold Drawing:
- 5140 steel wires drawn to ±0.005 mm tolerance for precision springs (surface finish: Ra 0.2 μm via polishing).
- Energy Efficiency: 95% reduction in cross-sectional area with 25% elongation.
Applications of High Carbon Steel
Industry | Applications | Preferred Grades |
---|---|---|
Cutting Tools | Knives, drills, saw blades | 1095, W1 |
Automotive | Springs, bearings | 52100, 1060 |
Construction | High-strength cables, rebars | 1080, 1075 |
Industrial Machinery | Gears, shafts | 1060, 1095 |
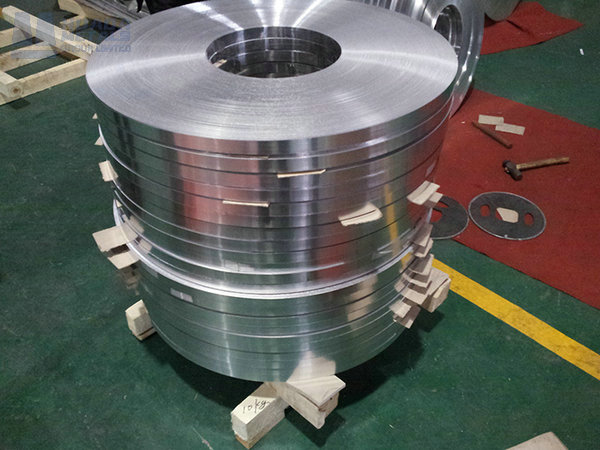
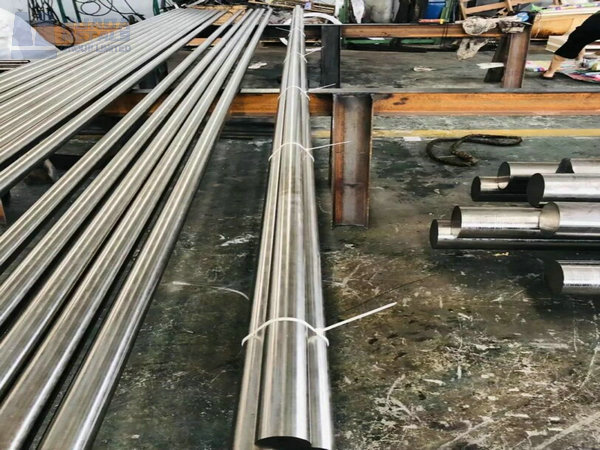
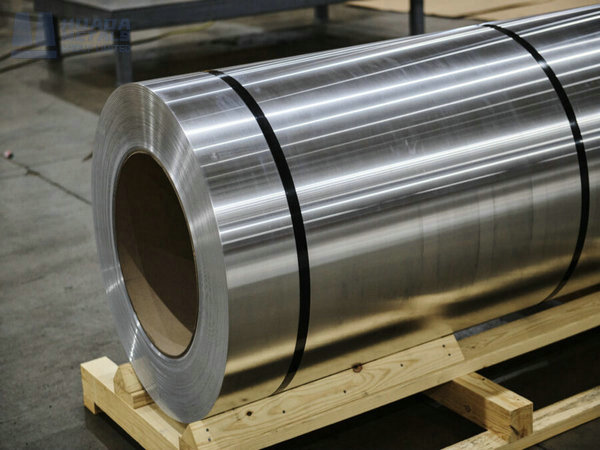
Cost Structure
Material | Raw Material Cost | Heat Treatment Cost | Machining Cost |
---|---|---|---|
1060 | 1.5−1.5−2.5 | 0.5−0.5−1.5 | 1.0−1.0−2.0 |
1095 | 2.0−2.0−3.5 | 1.0−1.0−2.0 | 1.5−1.5−3.0 |
52100 | 3.0−3.0−5.0 | 1.5−1.5−3.0 | 2.0−2.0−4.0 |
Tool Steel D2 | 5.0−5.0−8.0 | 2.0−2.0−4.0 | 3.0−3.0−6.0 |
High Carbon Steel
Property | High Carbon Steel | Stainless Steel 304 | Alloy Steel 4140 |
---|---|---|---|
Hardness (HRC) | 60-67 | 20-25 | 28-32 (HRC) |
Wear Resistance | ★★★★★ | ★★ | ★★★ |
Corrosion Resistance | ★★ | ★★★★★ | ★★★ |
Cost Efficiency | ★★★★ | ★★ | ★★★ |
In Conclusion
High carbon steel remains a critical material for applications requiring extreme hardness, wear resistance, and cutting performance.
Key Takeaways:
Best for cutting tools & high-stress components (1095, 52100)
More cost-effective than alloy/tool steels for many applications
Requires proper heat treatment for optimal performance
High carbon steel remains a cornerstone of industrial manufacturing due to its unmatched hardness, wear resistance, and cost efficiency. While its poor weldability and low toughness at elevated temperatures pose challenges, these are mitigated by advanced heat treatments and alloy design. HuaDa Metals has the good quality products in medium carbon steel, and the service is customerized for every clients, please contact us or ask for the lastest price.