Ferritic stainless steels (FSS) constitute a critical subgroup of stainless steels, characterized by a body-centered cubic (BCC) crystal structure and a nominal chromium content of 10.5–30 wt%. Unlike their austenitic counterparts, FSS are low in nickel (Ni) or nickel-free, relying instead on chromium and stabilizing elements like aluminum (Al), titanium (Ti), or niobium (Nb) to maintain their ferritic phase. This composition imparts excellent corrosion resistance, thermal stability, and cost-efficiency, making FSS indispensable in applications prioritizing oxidation resistance, formability, and reduced thermal expansion.
Ferritic stainless steels are chromium-based alloys (10.5-30% Cr) with a body-centered cubic (BCC) structure, offering excellent stress corrosion cracking resistance and moderate corrosion protection at lower costs than austenitic grades. These magnetic steels are characterized by:
No nickel content (unlike austenitics) for better price stability
Limited low-temperature toughness (ductile-brittle transition occurs)
Superior resistance to chloride SCC vs. 304/316 stainless
Microstructural Fundamentals of Ferritic Stainless Steel
FSS retain their BCC structure across all temperatures due to:
- Low stacking fault energy (SFE): Inhibits twinning and phase transformations (unlike FCC austenite).
- Thermal stability: No γ→α phase transition (unlike martensitic steels), ensuring dimensional consistency in heat-affected zones (HAZ).
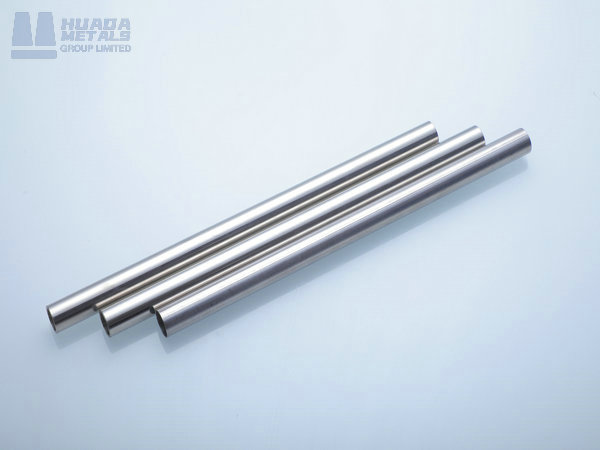
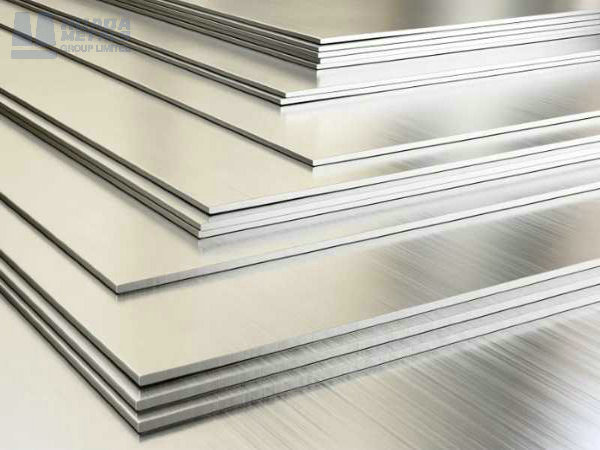
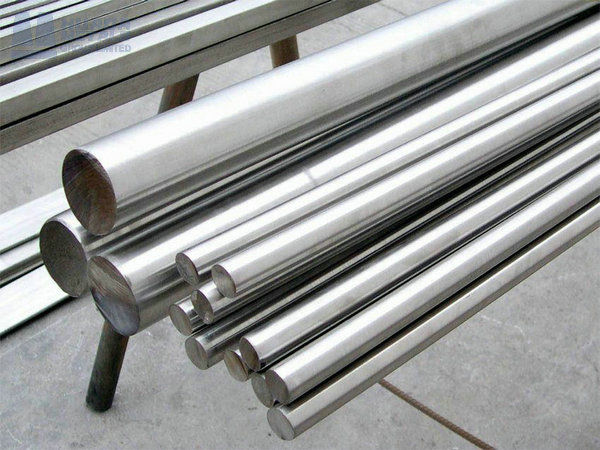
Chemical Composition of Ferritic Stainless Steel
Grade | UNS | Cr% | C% | Mo% | Other | PREN¹ |
---|---|---|---|---|---|---|
430 | S43000 | 16-18 | ≤0.12 | – | – | 17 |
434 | S43400 | 16-18 | ≤0.12 | 0.9-1.4 | – | 22 |
439 | S43035 | 17-19 | ≤0.03 | – | Ti 0.20+4(C+N) | 18 |
444 | S44400 | 17-20 | ≤0.03 | 1.8-2.5 | Nb+Ti 8×C min | 26 |
446 | S44600 | 23-27 | ≤0.20 | – | N≤0.25 | 27 |
Physical Properties of Ferritic Staninless Steel
Property | 430 | 439 | 444 |
---|---|---|---|
Density (g/cm³) | 7.70 | 7.70 | 7.75 |
Melting Range (°C) | 1425-1510 | 1420-1480 | 1420-1480 |
Thermal Conductivity (W/m·K) | 26.0 | 25.0 | 24.5 |
Electrical Resistivity (μΩ·m) | 0.60 | 0.65 | 0.70 |
CTE (20-100°C, μm/m·°C) | 10.4 | 10.5 | 10.3 |
- Density: 7.7–7.9 g/cm³ (5–10% lighter than austenitic grades).
- Thermal Conductivity: 24–30 W/m·K (40–60% higher than 304 stainless, ideal for heat exchangers).
- Coefficient of Thermal Expansion (CTE): 10–12 × 10⁻⁶/K (matches ferrous alloys, minimizing thermal stress in bimetallic assemblies).
- Magnetic Properties: Strongly ferromagnetic (critical for electromagnetic applications).
Mechanical Properties of Ferritic Staninless Steel
Grade | YS (MPa) | UTS (MPa) | Elongation (%) | Hardness (HB) |
---|---|---|---|---|
430 | 310 | 450 | 20 | 160 |
439 | 275 | 415 | 22 | 150 |
444 | 345 | 515 | 20 | 180 |
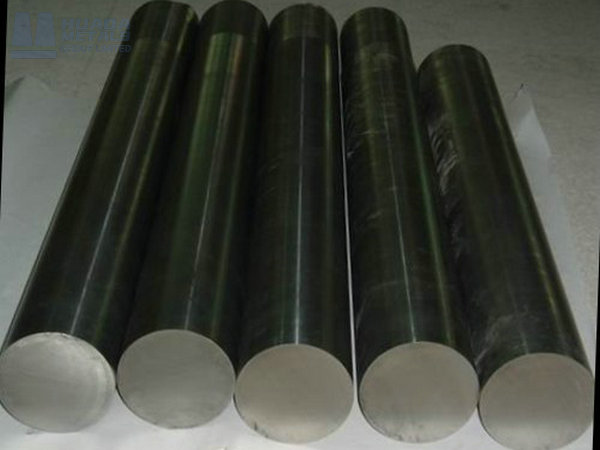
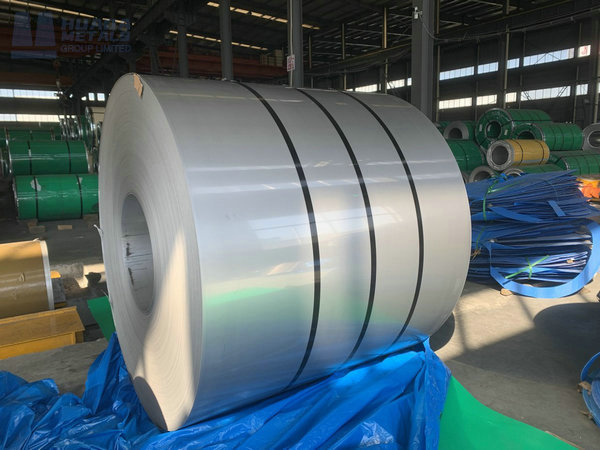
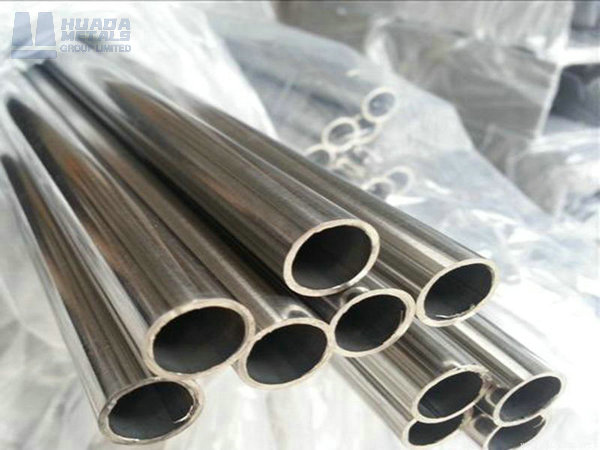
- Yield Strength (YS): 200–450 MPa (higher than austenitic grades in annealed condition).
- Tensile Strength (TS): 400–600 MPa (enhanced by cold working, but with limited strain hardening).
- Elongation: 15–30% (reduced at higher Cr content due to embrittlement).
- Hardness: 150–220 HB (Brinell) or 170–250 HV (Vickers).
- Impact Toughness: Moderate (20–50 J at room temperature); declines sharply below −20°C (brittle fracture-prone).
Key Advantages of Ferritic Stainless Steel
- Corrosion Resistance:
- Uniform corrosion: Resists atmospheric, mild acidic, and alkaline environments (e.g., 430 in automotive exhausts).
- Stress corrosion cracking (SCC): Immune in chloride media (unlike austenitic 304/316).
- Pitting/crevice corrosion: Improved by Mo addition (e.g., 444 in seawater desalination).
- Thermal Performance:
- High-temperature oxidation: Retains strength up to 800–950°C (e.g., 430Ti in furnace linings).
- Creep resistance: Enhanced by Nb (e.g., 441 in automotive catalytic converters).
- Cost Efficiency:
- Nickel-free composition: 20–40% cheaper than 304/316L.
- Resource sustainability: Lower critical raw material dependency.
Applications of Ferritic Stainless Steel
- Automotive:
- Exhaust systems: 409L (low-Cr, Ti-stabilized) for mufflers and catalytic converter casings.
- Fuel rail components: 430 for corrosion resistance in ethanol-blended fuels.
- Architectural/Construction:
- Roofing/cladding: 430 (painted) for cost-effective aesthetics.
- Industrial kitchens: 430 (magnetic, scratch-resistant) for equipment panels.
- Energy:
- Solar water heaters: 444 (Mo-alloyed) for high-temperature collectors.
- Biomass boilers: 441 (Nb-stabilized) for superheater tubes.
- Consumer Goods:
- Kitchenware: 430 (non-magnetic, cost-effective) for sinks and cutlery.
- Appliances: 439 (ultra-low C) for dishwasher interiors.
Manufacturing Costs and Processing Considerations
Cost Drivers
- Raw materials: Chromium (20–30% of cost) vs. nickel (40–60% in austenitic grades).
- Stabilizer additions: Ti/Nb (0.5–1.5% premium) vs. nickel-free 430 (baseline).
- Surface finishing: Passivation (5–10% cost increase) for critical applications.
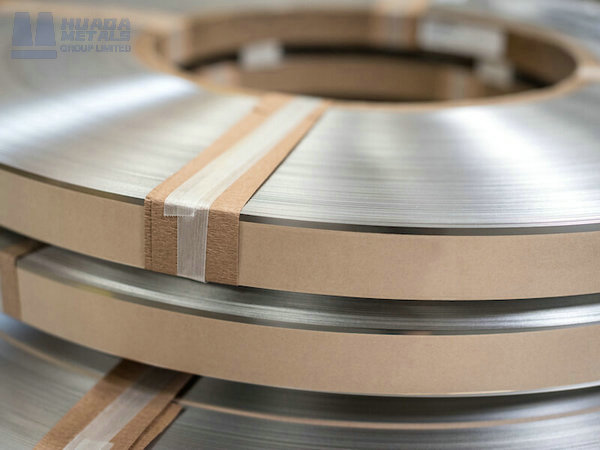
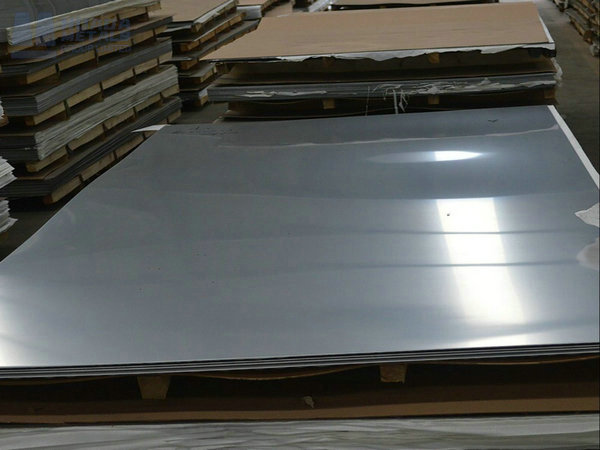
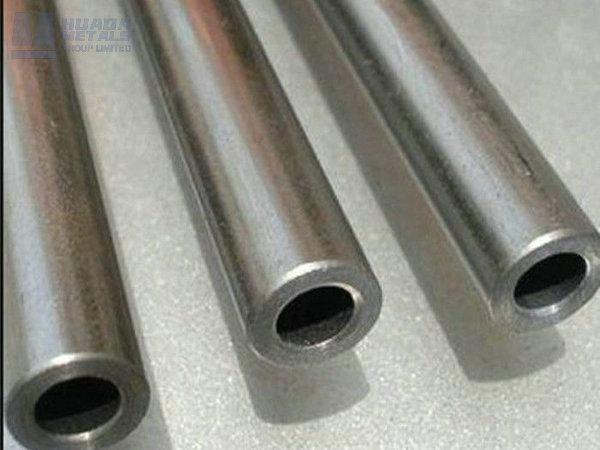
Key Manufacturing Processes
- Hot/Cold Rolling:
- Thin gauges: 430 annealed to 0.3–1.0 mm for deep drawing.
- Textured surfaces: Cold-rolled 439 with 2B finish for decorative panels.
- Welding:
- Shielded metal arc (SMAW): ER308L filler for 430 (mitigates 475°C embrittlement).
- Laser welding: Preferred for automotive exhausts (minimizes HAZ grain growth).
- Heat Treatment:
- Solution annealing: 800–900°C (recrystallization for corrosion resistance).
- Stress relief: 300–400°C (after forming to prevent distortion).
Advanced Fabrication Techniques
- Powder Metallurgy (PM):
- Metal injection molding (MIM): 430L for complex gears (density ≥98% theoretical).
- Hot isostatic pressing (HIP): 444 for turbine blades (near-net-shape, reduced machining).
- Additive Manufacturing (AM):
- Directed energy deposition (DED): 430L for repair of industrial burners.
- Binder jetting: 439 for catalytic converter substrates (porosity control).
In Conclusion
Ferritic stainless steels represent a cost-effective alternative to austenitic grades, offering good corrosion resistance and unique properties for specific applications. These chromium-based alloys (10.5-30% Cr) feature a body-centered cubic structure that provides excellent resistance to stress corrosion cracking and moderate general corrosion protection. While lacking nickel content makes them more affordable and price-stable, it also limits their formability and low-temperature toughness compared to austenitic grades. Key advantages include superior chloride SCC resistance, lower thermal expansion (≈40% less than 304), and better machinability.
Ferritic stainless steels occupy a unique niche in materials engineering, offering an unmatched combination of corrosion resistance, thermal stability, and cost efficiency. While their brittleness at low temperatures and limited weldability pose challenges, advancements in ultra-low-carbon chemistry (e.g., 439, 441) and additive manufacturing are expanding their applications. From automotive exhausts to solar thermal systems, FSS remain the alloy of choice for industries demanding sustainable, high-performance solutions in non-cryogenic environments. HuaDa Metals has the good quality products and contact us.